Форма кузова. С целью выбора наилучшей аэродинамической формы вагонов поезда и определения минимального коэффициента воздушного сопротивления институтом механики МГУ и Харьковским авиационным институтом были проведены специальные исследования моделей головного вагона в аэродинамической трубе. Аэродинамические исследования показали, что по характеру обтекаемости должна быть принята такая модель, которая обеспечивает в скоростном электропоезде коэффициент воздушного сопротивления Сх=0,3 и менее. На основании проведенных исследований, а также с учетом целесообразной технологичности изготовления выбранная форма головного вагона электропоезда ЭР200 характеризуется достаточно малым коэффициентом воздушного сопротивления, равным 0,292, а силуэт лобовой части отвечает современным требованиям технической эстетики.
Для обеспечения необходимой жесткости кузова, уменьшения давления воздуха на стекла окон при встречном движении поездов, рационального использования внутривагонного пространства и снижения массы тары вагона боковые стены наклонены внутрь вагона. Кабина машиниста несколько отодвинута назад, что помимо удовлетворения требований аэродинамики, обеспечивает повышение безопасности локомотивной бригады. На всех вагонах поезда для снижения воздушного сопротивления установлены фальшборта, закрывающие подвагонное оборудование между тележками, а промежутки между вагонами перекрыты по контуру специальным резиновым шатром.
Материал кузова. Для обеспечения допустимой нагрузки на ось масса тары моторного вагона с его мощным и сложным электрооборудованием должна быть минимальной. Обычно 18—20% массы моторного вагона приходится на кузов, поэтому при проектировании металлического кузова особое внимание было уделено снижению его массы.
В качестве основного материала для несущих конструкций кузовов вагонов пригородных электропоездов применяют углеродистую сталь, которая, однако, имеет большую массу, низкую удельную прочность и слабое сопротивление коррозии. Для снижения массы кузова перспективным является использование в его конструкции новых материалов, имеющих более высокий показатель удельной прочности. Существует ряд материалов, таких как нержавеющие стали и алюминиевые сплавы, которые достаточно хороши для применения их в кузовах вагонов. В частности, алюминиевые сплавы отличаются от углеродистых сталей высокой прочностью при низкой плотности, повышенной коррозионной стойкостью, значительной сопротивляемостью абразивному износу. Однако модуль упругости алюминиевых сплавов почти в 3 раза меньше, чем у стали, поэтому для устранения опасности потери устойчивости элементов конструкции, изготовленной из алюминиевого сплава, требуется некоторое увеличение их площади сечения. Низкий модуль упругости алюминиевых сплавов имеет и свои достоинства: кузова из алюминиевых сплавов обладают в 3 раза большей энергоемкостью по сравнению со стальными равного сечения и прочности и, следовательно, повышенной способностью к поглощению удара. Кроме того, алюминиевые сплавы хорошо поддаются обработке резанием и давлением.
Это делает алюминий весьма перспективным конструктивным материалом для применения в подвижном составе железнодорожного транспорта.
Однако из-за сравнительно высокой стоимости алюминия, а также технологической сложности работы с ним (необходимо проведение тщательной, подготовки листов и профилей к сварке в среде газа аргона, требуется специальная оснастка при сварке узлов и др.) этот материал пока не получил широкого применения в вагоностроении.
Так как недостатки алюминиевых сплавов весьма незначительны по сравнению с рядом их ценных преимуществ, главное из которых — возможность достижения минимальной массы силовых конструкций, для кузовов электропоезда ЭР200 применены алюминиевые сплавы. Постройка алюминиевого кузова показала, что его масса на 35—40% меньше массы стального кузова таких же габаритов.
Сравним массу узлов алюминиевого кузова электропоезда ЭР200 с массой узлов стального кузова электропоезда ЭР22 (длина 24,5 м):
Узел кузова | Масса кузова, кг | Узел кузова | Масса кузова, кг | ||
ЭР2 2 | ЭР200 | ЭР22 | ЭР200 | ||
Рама с полом | 6 520 | 3800 | Стена торцовая | 480 | 280 |
Боковые стены | 3 220 | 1550 | Стена лобовая | 690 | 515 |
Крыша | 1 990 | 1185 | Кузов в сборе | 12 900 | 7330 |
РВЗ совместно с ВНИИ вагоностроения и институтом электросварки им. Патона провели научно-исследовательские и опытноконструкторские работы как по выбору марки алюминиевого сплава, так и по технологии сварки, прочностным характеристикам кузова, способности его сопротивляться ударным нагрузкам. Для изготовления кузовов вагонов электропоезда ЭР200 приняты алюминиевые сплавы марок АМг5, АМг6 и 1915 (ГОСТ 4784—77).
У сплава 1915 по сравнению со сплавом АМг6 более высокие прочностные характеристики. Из него можно получить более сложные и тонкостенные профили и панели при скорости прессования в 10 раз большей, чем из сплава АМг6. Стоимость прессованных профилей из сплава 1915 на 10% ниже. Из сплава 1915 изготовлены боковины, поперечные балки и раскосы рамы, поперечные элементы жесткости стен и крыши кузова электропоезда ЭР200, из сплава АМг5 — обшивка кузова, листы пола, а из сплава АМг6 — шкворневые и буферные балки рамы.
Наряду с отмеченными преимуществами алюминиевые сплавы имеют недостатки, обусловленные их физическими свойствами. Эти сплавы характеризуются высокой теплопроводностью и теплостойкостью, большой скрытой теплотой плавления. Для их расплавления требуются мощные источники тепла. При нагреве выше 400° С снижаются прочность и пластичность, что приводит к проседанию металла в зоне нагрева и вызывает необходимость применения технологических подкладок и прижатия. Коэффициент линейного расширения алюминиевых сплавов более чем в 2 раза превышает этот показатель для стали. При переходе из жидкого состояния в твердое эти сплавы имеют гораздо большую усадку. Указанные свойства обусловливают высокую склонность конструкций из алюминиевых сплавов к деформированию вследствие неравномерного нагрева при сварке (при прочих равных условиях в 1,5—2 раза больше, чем в стальных конструкциях).
Для тонколистовых конструкций характерно появление при сварке деформирования поверхности, что снижает ее несущую способность и ухудшает внешний вид.
Деформации обшивки (выпучивание) могут быть предотвращены или уменьшены применением соответствующего технологического процесса изготовления и выбором более рациональной конструкции.
Так как кузов электропоезда ЭР200 имеет ряд крупногабаритных сварных конструкций (раму, металлический пол, боковые стены, крышу, торцовые стены), которые обладают весьма большой склонностью к деформированию, основные элементы и узлы кузова изготовляли, применяя специально созданную оснастку. Сварке кузова предшествовала длительная подготовка производства. Была выполнена разбивка всей свариваемой конструкции кузова на отдельные элементы, узлы и сборки; были разработаны сборочносварочные стенды для крупных узлов, определяющих геометрию изделия, и определены допустимые зазоры при сборке, технологические припуски на укорочение свариваемых элементов и порядок наложения сварных швов.
Сварку, где это возможно, осуществляли без разделки кромок либо применяли Х-образную разделку с минимальным усилением шва. В отдельных случаях деталям придавали обратный выгиб. Учитывали последовательность наложения швов. При наличии в узле стыковых и угловых швов в первую очередь сваривали стыковые швы.
Результаты испытаний алюминиевого кузова. После изготовления кузов был подвергнут прочностным испытаниям. В программу испытаний входили: воздействие вертикальной статической нагрузки брутто кузова, продольное сжатие по автосцепным приборам усилием 2500 Н, вертикальная нагрузка, равная 1,5 брутто кузова (последняя для оценки устойчивости тонкостенных элементов кузова при действии одновременно статических и динамических эксплуатационных нагрузок).
Напряжения от отдельных видов испытательных нагрузок и суммарные напряжения от эксплуатационных нагрузок не превысили допустимых и все элементы кузова работали в стадии упругих деформаций.
При вертикальной нагрузке 1,5 брутто кузова не наблюдалось потери устойчивости кузова и его отдельных тонкостенных элементов.
Жесткость кузова характеризует максимальный прогиб среднего сечения от нагрузки брутто, который равен 7,5 мм. О запасе прочности можно судить еще и по напряжениям во всех сечениях кузова, которые по I расчетному режиму не превышают 8700 Н/см2, что составляет 58% от предела текучести для сплава- АМг5 (15 000 Н/см2), а по III расчетному режиму не превышают 6950 Н/см2, что составляет 67,5% от допустимых по III расчетному режиму (10 300 Н/см2).
С целью определения частот собственных колебаний кузова и его элементов проведены вибрационные испытания. Вибрации возбуждались пневматическим вибратором, устанавливаемым как по середине кузова, так и на консолях. Эти испытания показали, что собственная частота изгибных колебаний кузова равна примерно 6 Гц.
Для определения несущей способности кузова из алюминиевых сплавов при действии продольных ударных нагрузок были проведены испытания на соударение опытного кузова на экспериментальном кольце ВНИИЖТ. Было установлено, что конструкция алюминиевого кузова обладает достаточной прочностью к восприятию ударных нагрузок, возникающих при аварийных столкновениях составов со скоростью до 20 км/ч.
Во время комплексных испытаний электропоезда ЭР200 со скоростями движения до 200 км/ч были выполнены динамические прочностные испытания кузова, при которых определили напряжения в средней части и в зоне соединения консольной части кузова с шкворневой балкой. Испытания показали, что конструкция кузова удовлетворяет условию минимально допустимой усталостной прочности, оцениваемой по методике ВНИИЖТ (коэффициент запаса усталостной прочности не менее 2,0).
Вынужденные колебания кузова на стыках рельсов, уложенных в уравнительных соединениях на участках бесстыкового пути линии Ленинград—Москва, характеризуются частотами 3—4,5 Гц при скоростях движения 135—200 км/ч, а при отдельных биениях имеют место всплески напряжений на частотах 6—7,5 Гц.
Динамические ходовые испытания показали, что вследствие недостаточной изгибной жесткости алюминиевого кузова (частота основного топа изгибных колебаний ниже 8 Гц) показатели плавности хода моторного вагона в вертикальной плоскости при скорости 200 км/ч достигают 3,45, т. е. по условиям комфорта превышают допустимый уровень (3,25). Следует отметить, что при скорости движения до 160 км/ч показатели плавности хода в вертикальной плоскости не превышают допустимого уровня.
Для выполнения нормативного требования к конструкции кузова о несовпадении частоты основного тона его изгпбных колебаний с частотой подпрыгивания (галопирования) тележки частота основного тона изгибных колебаний кузова моторного вагона должна быть увеличена примерно до 10 Гц путем увеличения его изгибной жесткости. В настоящее время ведется поиск наиболее рациональных методов дальнейшего совершенствования алюминиевых элементов кузова с учетом влияния возможных изменений конструкции на весовые показатели, которые могут при этом ухудшиться, и в сравнении с основными технико-экономическими показателями для стального кузова.
Конструкция кузова. Кузов вагона представляет собой замкнутую оболочку (рис. 15) с вырезами для оконных и дверных проемов. Он состоит из продольных (боковые балки рамы, верхние обвязочные профили боковых стен, гофры боковых стен и крыши) и поперечных (стойки боковых стен, дуги крыши и поперечные балки рамы) элементов жесткости, которые связаны между собой тонколистовой обшивкой (рис. 16). Такая конструкция кузова позволяет включить в работу все его элементы.
Конструкция кузова вагона включает в себя следующие крупногабаритные узлы: раму, пол, крышу, боковые и торцовые стены. Сварная рама (без хребтовой балки) собрана из двух консольных частей, двух продольных элементов (прессованные профили прямоугольного сечения) и набора поперечных балок.
Консоли кузовов моторных вагонов и задняя консоль кузовов головных вагонов одинаковы и только передняя консоль кузова головного вагона выполнена несколько иначе. Последнее вызвано установкой по продольной оси передней консоли центральной балки, в которой вмонтирована автосцепка СА-3 с резинометаллическим поглощающим аппаратом. Центральная балка соединена с одной стороны с буферной балкой, а с другой — через раскосы со шкворневой балкой.
Остальные консоли кузова не имеют центральных балок и передача продольной нагрузки от буферной балки на шкворневую и далее на продольные элементы рамы происходит непосредственно через раскосы. Буферные и шкворневые балки, а также центральная балка головного вагона сварены из листов толщиной 10—14 мм, а раскосы выполнены из прессованного профиля коробчатого сечения высотой 170, шириной 195 и толщиной стенки 12 мм. Поперечные балки рамы изготовлены из прессованного швеллерообразного профиля с высотой стенки 120 мм и шириной полки 60 мм.
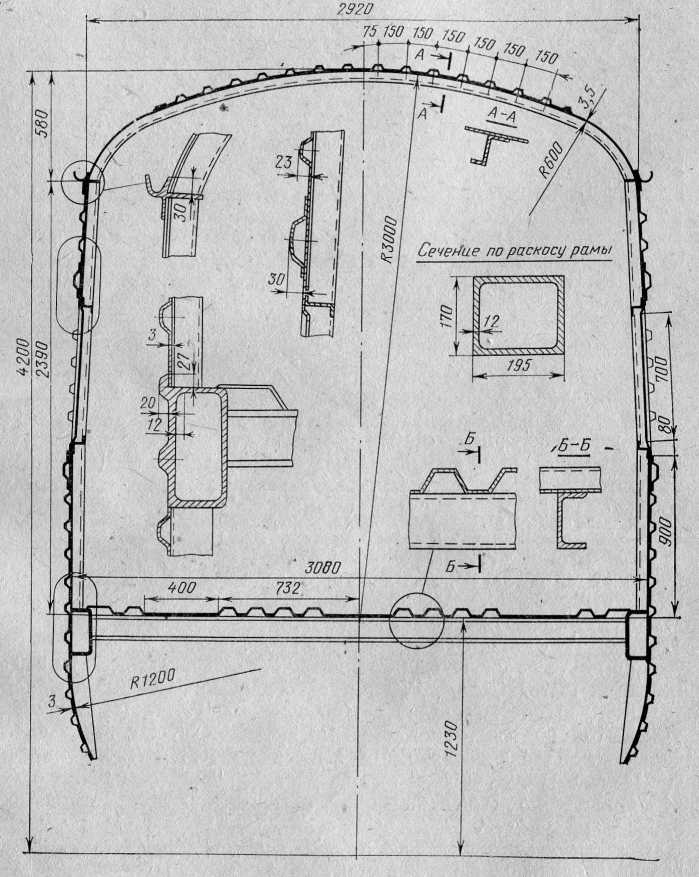
Рис. 15. Сечение кузова вагона
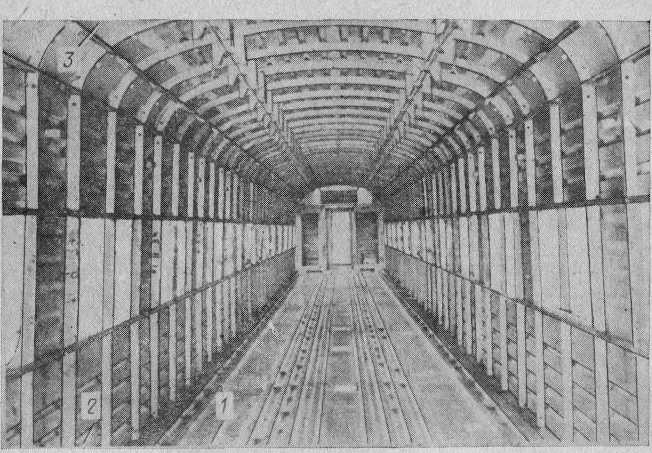
Рис. 16. Кузов вагона (вид изнутри): 1 — рама; 2 — боковая стена; 3 — крыша
Сборку как отдельных узлов, так и рамы в целом осуществляют в специальных кондукторах.
Сваренная рама кузова сверху покрыта несущим полом, собираемым из гофрированных листов толщиной 2 мм. В полу предусмотрены три широких желоба, куда при сборке вагона укладывают провода электропроводки. Соединение стыков листов осуществляют только на поперечных балках рамы. Листы пола к балкам рамы приваривают электрозаклепками. Расположение гофров в листах пола по всей длине рамы обеспечивает полное включение пола в работу кузова, причем пол воспринимает и значительные продольные усилия.
Крыша выполнена из гофрированного листа, подкрепленного изнутри потолочными дугами, и собирается из отдельных, заранее изготовленных секций длиной около 3,5 м. Каждая секция включает в себя среднюю часть крыши (на участке большого радиуса) и два ската. Средняя часть собирается из двух листов толщиной 2 мм и имеет 14 гофров с шагом 170 мм. Скаты крыши для придания большей жесткости выполнены небольшим радиусом и обшиты гладким листом толщиной 3 мм. Дуги изготовлены из прессованного Z-образного профиля и приварены к листам секций точечной контактной сваркой.
Боковая стена кузова выполнена из гофрированных листов толщиной 3 мм, армированных горизонтальными и вертикальными элементами жесткости. Все элементы жесткости изготовлены из прессованных профилей Z-образного сечения, за исключением верхнего продольного обвязочного профиля, имеющего Т-образную форму. При сборке боковых стен первоначально собирают стойки оконных и дверных проемов. Профили и стойки соединяют с гофрированными листами обшивки контактной точечной сваркой.
Торцовая стена имеет каркас, сваренный из прессованных профилей швеллерообразного сечения, который обшит гофрированным листом толщиной 3 мм. Каркас лобовой стены головного вагона выполнен из прессованных профилей различных сечений. В передней части стены расположены две сварные вертикальные балки.
Для передачи усилия от вертикальных стоек на стойки боковых стен, раму и крышу под окнами лобовой стены смонтирована основная горизонтальная балка. В каркас входит также ряд вертикальных и горизонтальных профилей, придающих лобовой стене головного вагона необходимую форму. Снаружи каркас обшит листом толщиной 2 мм.
На лобовой стене головного вагона установлена серийная автосцепка СА-3.
На торцовых стенах всех моторных вагонов и торцовой стене головного вагона установлена облегченная жесткая автосцепка. Она предназначена для жесткой автоматической сцепки вагонов внутри состава и передачи на опорные части шкворневой балки ударно-тяговых усилий. Эта автосцепка состоит из головки 1 (рис. 17) с механизмом сцепления, корпуса гасителя 3 с резинометаллическими элементами 4, обеспечивающими ход 45 мм при усилии 250 кН, и центрирующего устройства 5 для фиксации автосцепки по продольной оси вагона. Шток амортизатора через ось шарнирно соединен с переходником. Последний двумя пластинчатыми рессорами удерживает головку в горизонтальном положении, но позволяет ей занимать различные положения относительно вертикальной оси. Для расцепления автосцепки она оборудована механизмом расцепления 2.
Разгрузка оси и гасителя при усилии сжатия более 250 кН осуществляется упором переходника в корпус гасителя после полного хода 45 мм. Шток от вращения удерживается закрепленными на нем шпонками, скользящими в пазах корпуса гасителя.
Автосцепка в сборе устанавливается на консоли рамы кузова с помощью цапф крепления автосцепки, которые входят в соответствующие отверстия корпуса гасителя и совместно образуют ось вращения. Автосцепка удерживается вдоль вагона центрирующим устройством 5, которое представляет собой пружинный элемент, шарнирно соединенный с проушиной корпуса гасителя и рамой вагона.
Расцепление вагонов осуществляют вручную путем вытягивания расцепного привода одной головки. При этом механизмы обеих головок поворачиваются на 60° и блокирующие тяги запираются защелками, благодаря чему механизмы сцепления головок удерживаются в расцепленном положении. Рукоятку после расцепления головок навешивают на крючок под головкой. Сцепление головок при толкании вагона на вагон происходит автоматически при любом положении механизмов в головках.
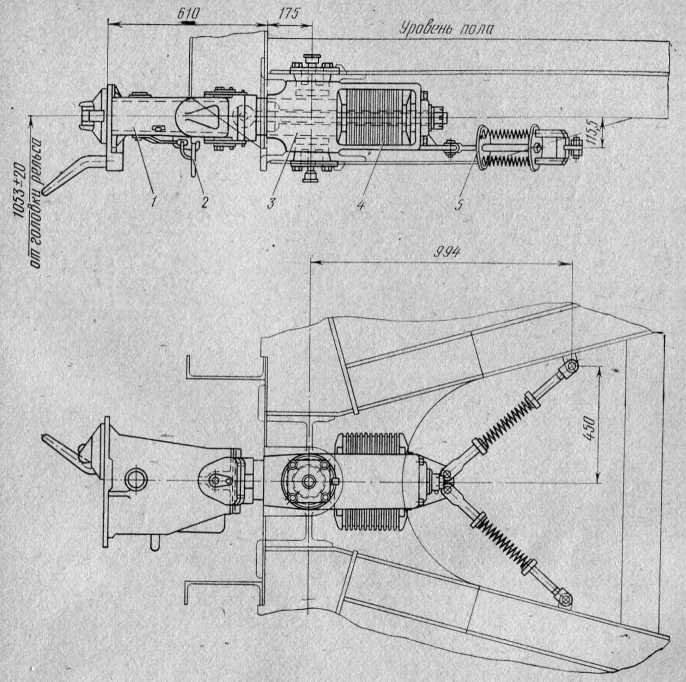
Рис. 17. Облегченная жесткая автосцепка
Для транспортирования отдельных вагонов электропоезда ЭР200 к головке жесткой автосцепки присоединяют двумя болтами специальное приспособление, которое сцепляется с автосцепкой СА-3 любого другого подвижного состава.
Внутренние конструкции вагона. Внутренние конструкции вагона включают в себя пол, потолок, боковые, торцовые и поперечные стены, а также шкафы и перегородки. Для снижения шума и вибраций кузов с внутренней стороны покрыт слоем противошумной мастики, на металлический пол дополнительно нанесен слой асбестовой изоляции толщиной 4—5 мм, элементы внутренних конструкций соединены с кузовом через резиновые прокладки толщиной 3 мм, а обрешетка пола — посредством резиновых втулок высотой 15 мм. Тепло- и звукоизоляция выполнена из пенопласта и пенополиуретана. Полки металлических оконных стоек и потолочных дуг оклеены пакетами из теплоизоляционного материала. На пол, боковые стены и потолок (поверх изоляции) в качестве гидроизоляционного слоя наклеена полиамидная пленка.
Пол покрыт щитами из столярных плит толщиной 19 мм и линолеумом, а стены и потолок облицованы декоративным бумажнослоистым пластиком светлых тонов.
В пассажирском салоне поверх линолеума дополнительно настелен синтетический ворсистый ковер. Общая толщина пола в салоне 130, а боковых стен — 95 мм.
Торцовые стены представляют собой шкафы для размещения электрооборудования. Стены и двери шкафов выполнены из алюминиевых сплавов и облицованы со стороны тамбура Декоративным пластиком. В шкафах изнутри для утепления и противопожарной безопасности нанесен слой асбестовой изоляции толщиной 3—4 мм. Перегородки служебных помещений изготовлены из столярных плит, облицованных с обеих сторон декоративным пластиком.
Внутреннее оборудование вагона включает в себя двери, окна, кресла, санузлы. Две входные двери расположены по концам вагона с обеих его сторон. Они выполнены поворотными, одностворчатыми с уплотнением по контуру. В конце головного вагона и по концам моторных вагонов расположены торцовые двери, предназначенные для перехода обслуживающего персонала и пассажиров из вагона в вагон. Эти двери отличаются друг от друга наличием в верхней части либо стекла, либо зеркала.
Передняя часть кабины машиниста выполнена остекленной. Окна кабины изготовлены из безосколочных стекол, не поддающихся абразивному воздействию и не влияющих на нормальное восприятие цветовых сигналов. Окна обеспечивают хорошую видимость в условиях эксплуатации электропоезда при температурах от + 60 до — 40° С.
В целях равномерного обогрева лобовых окон зимой, предотвращения запотевания и образования на них инея предусмотрен пленочный электрообогрев стекол. Герметично запрессованное в металлические рамки стекло (триплекс) состоит из двух закаленных пластин, склеенных прозрачной эластичной прокладкой, обеспечивающей безосколочность панели при механических повреждениях и являющейся одновременно изолирующей прокладкой между двумя нагревательными элементами панели. Электропитание к нагревательным элементам панели подается от сети постоянного тока напряжением НО В. Панели имеют три режима работы. Когда оба нагревательных элемента включены параллельно, осуществляется режим «Интенсивный нагрев», который использует при низких минусовых температурах. «Нормальный нагрев» и «Слабый подогрев» осуществляются разными вариантами подключения нагревательных элементов.
Окно пассажирского салона представляет собой пакет, состоящий из наружной и внутренней алюминиевых рамок с безосколочными стеклами, армированными резиновым профилем. Между рамками смонтирован пластмассовый профиль, во внутреннюю полость которого заложено влагопоглощающее вещество. Для обеспечения герметичности окна пространство между каждой рамкой и пластмассовым профилем промазано специальным герметиком. Текстолистовая прокладка и пластмассовый профиль служат для предохранения окна и стены вагона от промерзания. Окно устанавливают снаружи вагона в оконный проем кузова, армированный резиновым профилем. Окна салона подразделяются на глухие неоткрывающиеся и с открывающейся форточкой; последних по два с каждой стороны вагона.
В пассажирском салоне установлены мягкие двухместные поворотные кресла с откидывающейся спинкой (рис. 18). Основание кресла закреплено неподвижно к полу. Поворачивающаяся часть кресла имеет подушки для сидения, подлокотники и две независимые спинки. Спинка наклоняется в любое из трех положений при небольшом подъеме подлокотника вверх.
Для поворота кресла на 180° необходимо съемной рукояткой повернуть рычаг 4, расположенный у неподвижного основания со стороны центрального прохода. При этом зажимы, удерживающие верхнюю часть кресла, выводятся из зацепления и дают возможность повернуть кресло в любую сторону. Обратный поворот рычага закрепляет кресло в выбранном положении. Поворот кресел по ходу движения осуществляет проводник вагона перед выездом электропоезда на линию.
Каждый вагон электропоезда оборудован двумя туалетными помещениями, расположенными в тамбуре в одном конце вагона. Оборудование санузла состоит из бака для чистой воды, бака для подогрева воды, умывальника и унитаза с эвакуационным устройством. Бак для чистой воды емкостью 50 л расположен в верхней части туалетного помещения. Заполняют бак через наливную трубу, выходящую наружу под вагоном. Этот бак сообщается с баком для подогрева воды, причем последний имеет емкость примерно 2,5 л. Оба бака соединены трубами с краном умывальника. Эвакуационное устройство унитаза имеет две трубы: широкую — фановую и узкую для смыва.
Вентиляция, кондиционирование, отопление и освещение. В систему вентиляции вагонов электропоезда входят: вентиляция пассажирского помещения, установка кондиционирования воздуха, вентиляция кабины машиниста, вентиляционные коробы -тяговых двигателей и преобразователя.
Вентиляция пассажирских салонов приточно-вытяжная. Она включает в себя мотор-вентиляторы, фильтры, потолочный и рециркуляционные каналы, жалюзи.
В потолочном канале смонтирован электрокалорифер, состоящий из двух секций. Между вентиляторами и калорифером установлен воздухоохладитель кондиционера. Предусмотрен один режим работы вентиляторов.
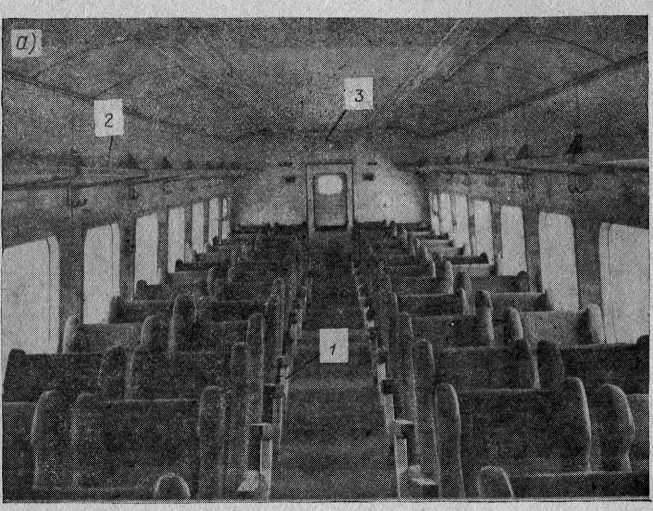
Рис. 18. Общий вид салона моторного вагона (а): 1 — кресло; 2 — багажная полка; 3 — указатель скорости и часы
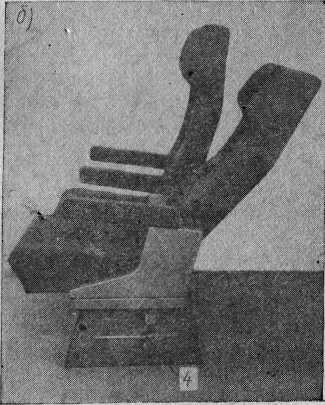
Рис. 18 Двухместное кресло (б) рычаг механизма поворота
Подача воздуха в пассажирское помещение составляет 5000 м3/ч, в том числе 1700 м3/ч свежего воздуха независимо от его наружной температуры, остальной воздух рециркуляционный. Вдоль вагона установлен потолочный вентиляционный канал, по которому воздух подается равномерно по всему салону. Рециркуляционный воздух по специальным каналам, расположенным над служебными помещениями, поступает в смесительные камеры, где смешивается со свежим и после фильтрации снова попадает в пассажирский салон.
На вагонах установлен кондиционер КЖВС-25 фреоновый, компрессорный, одноступенчатый, непосредственного испарения с воздушным охлаждением конденсатора. Холодопроизводительность кондиционера составляет 105 000 кДж/ч, что позволяет поддерживать температуру внутри вагона 22° С при наружной температуре до 32° С и относительной влажности до 70%.
Кондиционер состоит из нескольких отдельных узлов, соединенных между собой трубопроводами. Внутри вагона в чердачном помещении помещен воздухоохладитель. А компрессор, конденсатор и теплообменный фильтроосушительный аппарат размещены под вагоном.
Кондиционер работает следующим образом. Теплый воздух, проходя через воздухоохладители 4 (рис. 19), отдает свое тепло фреону, который, поглощая это тепло, кипит. Пары фреона отсасываются мотор-компрессором 7, сжимаются им до давления конденсации и нагнетаются в конденсатор 5. Здесь пары фреона сжижаются благодаря охлаждению их воздухом, продуваемым мотор-вентилятором 6 через батарею конденсатора. Жидкий фреон собирается в ресивере 7 и по трубопроводу поступает в теплообменный фильтроосушительный аппарат 3. В нем происходит дальнейшее охлаждение жидкого фреона парами, отсасываемыми компрессором из воздухоохладителя. Охлажденный жидкий фреон после прохождения через теплообменный аппарат поступает снова в воздухоохладитель через дросселирующее устройство. Приборы управления кондиционером размещены на щите 2.
В летний период кондиционированный воздух подается в кабину машиниста из потолочного канала пассажирского помещения. Забор воздуха для кабины осуществляется за воздухоохладительной установкой и с помощью специального мотор-вентилятора через систему каналов воздух поступает в кабину. Подача вентилятора составляет 700 м3/ч.
Для подогрева воздуха в зимнее время в шкафу задней стенки кабины установлен электрокалорифер. У выхода вентиляционного канала в кабину смонтирована заслонка, позволяющая осуществлять раздачу воздуха летом через отверстие в верхней части кабины, а зимой — снизу (у пола). Предусмотрен и рециркуляционный люк для забора воздуха из кабины. Зимой подача свежего воздуха в кабину составляет только 60 м3/ч.
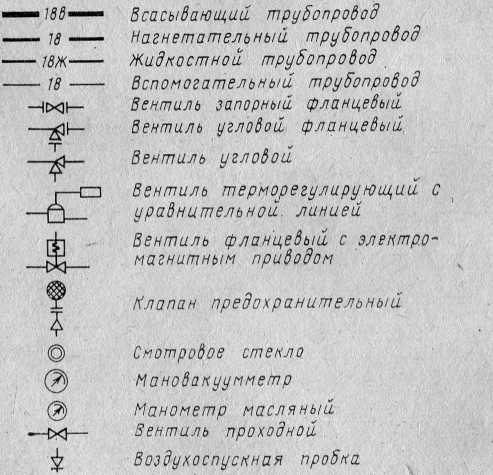
Рис. 19. Принципиальная схема кондиционера
Для подачи воздуха в тяговые двигатели в кузове моторного вагона имеются четыре подводящих вентиляционных канала с фильтровыми камерами. Воздух для охлаждения двигателей забирается через жалюзи в боковых стенах вагона, проходит через фильтр, установленный в нижней части канала, и затем поступает в гибкий рукав тягового двигателя. Нагретый двигателем теплый воздух выбрасывается в атмосферу. Для вентиляции преобразователя 3000/220 В, 50 Гц в фальшборте кузова имеется заборное отверстие для воздуха, а под рамой кузова для очистки воздуха установлена фильтровая камера, которая соединена с входным отверстием преобразователя гибким брезентовым патрубком. Подача воздуха для вентиляции преобразователя составляет около 1300 м3/ч.
Система отопления вагонов электропоезда состоит из электронагревательного устройства (печей) и электрокалориферов. Последние подогревают воздух, поступающий снаружи через потолочный канал.
Электронагревательное устройство включено в сеть с напряжением 3000 В. Оно установлено на полу вдоль боковых стен (в виде непрерывной линии) и состоит из трубчатых нагревательных элементов (рис. 20), смонтированных на высоковольтных фарфоровых изоляторах. Снаружи устройство перекрыто кожухом из перфорированного стального листа. Для защиты от случайного попадания на поверхность нагревательных элементов влаги, пыли и посторонних предметов предусмотрен специальный металлический экран. Общая мощность отопительных электронагревательных устройств головного вагона составляет примерно 22, моторного 25, а электрокалориферов 30 кВт. Такая высокая мощность отопительных приборов обеспечивает нормальные температурные условия в вагоне при наружной температуре до — 40° С.
Освещение пассажирского салона осуществляется люминесцентными лампами мощностью 40 Вт каждая с питанием от сети переменного тока напряжением 220 В, частотой 50 Гц. Светильники расположены на потолке, образуя две непрерывные линии. Освещенность пассажирского салона на уровне 0,8 м от пола составляет 200 — 250 лк. Для дежурного освещения в отдельных .светильниках каждого вагона дополнительно установлены лампы накаливания. Освещение в тамбурах и служебных помещениях, осуществляется только лампами накаливания.
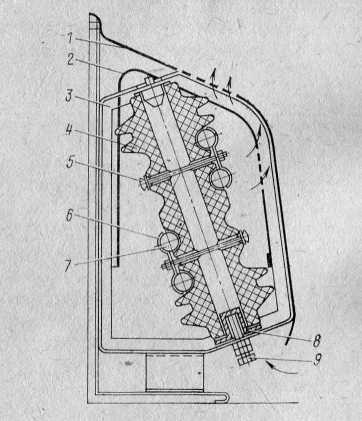
Рис. 20. Электронагревательное устройство: 1 — кожух; 2 — экран; 5 —-каркас; 4 — изолятор; 5 — шпилька; 6 — скоба; 7 — нагревательный элемент; 8 — втулка; 9 — натяжной болт