Профилактические и технические осмотры. Осмотр тележки необходимо производить в соответствии с правилами эксплуатации и должностными инструкциями. Кроме того, следует проверять состояние: подвесок (тяги, валики, серьги) и литого поддона; пружин центрального и буксового подвешивания; болтовых соединений (наличие гаек и шплинтов); предохранительных скоб тормозных траверс и надрессорного бруса; продольных тяг; гидравлических гасителей; опорных скользунов тележки (крепление коробок скользунов), допустимого износа вкладышей (ДСП-Г). Вкладыш-скользун должен равномерно выступать из коробки на высоту не менее 5 мм. Необходимо также проверять зазор а (см. рис. 18), который должен быть не менее 9 мм. Зазор менее 9 мм необходимо увеличить до величины 16±21 мм.
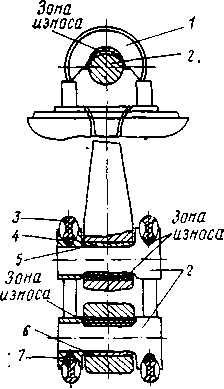
Рис. 20. Подвеска
Ремонт. В депо ремонтируют тележки при профилактических осмотрах и плановых ремонтах в соответствии с действующими правилами ремонта. После разборки тележек необходимо все узлы и детали очистить от грязи, масла и ржавчины. Для выявления степени износа деталей и узлов следует тщательно осмотреть и обмерить их.
При осмотре рамы необходимо проверить: состояние сварных швов; износ сколйзунов, втулок кронштейнов амортизаторов и кронштейнов подвешивания тормозной передачи; крепление шпинтонов к раме, а также состояние резьбы. Рамы, имеющие трещины в сварных швах и основном металле, к эксплуатации не допускаются.
После разборки тележки необходимо проверить состояние наружной и внутренней буксовых пружин, резиновых амортизаторов и опорного кольца; замерить износ деталей фрикционного гасителя, втулки, сухарей и колец; проверить резьбовые соединения.
Подлежат замене или восстановлению детали фрикционного гасителя при следующих величинах износа: втулка по наружному диаметру до 4 мм; кольцо по поверхности трения на глубину до 3 мм; сухарь по внутренней цилиндрической рабочей поверхности до 4 мм. При задирах или местной выработке на втулках и сухарях свыше 4 мм детали заменяют новыми. Детали с выкрошившейся резьбой и увеличенными зазорами следует заменить.
В центральном рессорном подвешивании необходимо тщательно проверить сварные швы бруса, а также определить величину износа вкладыша скользуна и проверить крепление на брусе подпятника, боковых и опорных скользунов, резиновые подкладки под скользуны. Если высота вкладыша (ДСП-Г) стала менее 25 мм, его заменяют.
Допускают к эксплуатации скользуны с мелкими питингами на поверхности трения, если они занимают не более 60% поверхности и глубина их не превышает 3 мм. Удалять задиры и риски разрешается механической обработкой.
Одновременно с проверкой вкладышей скользунов следует контролировать состояние опорных скользунов на шкворневой балке рамы вагона. Поверхность стального скользуна должна быть гладкой, без задиров, рисок и раковин. Удалять указанные дефекты разрешается механической обработкой, при этом толщина скользуна должна быть не менее 25 мм. В деталях стержня (см. рис. 18) и сварных швах поводка не должно быть трещин.
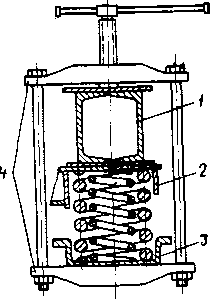
Рис. 21. Схема приспособления для замены пружин центрального подвешивания тележки: 1 — боковина рамы тележки; 2 — надрессорный брус; 3 — поддон; 4 — струбцина
Недопустимы выкрашивание и смятие резьбы на гайках и резьбовой части тяг 17, отслоение резины от армировки резино-металлических пакетов 19, трещины в армировочных тарелях.
Резиновые втулки головок гидрогасителей, имеющие разрывы, и валики с износом по диаметру свыше 1 мм заменяют новыми.
На всех трущихся поверхностях деталей подвески центрального подвешивания (тягах, валиках, серьгах) выкрашивание и задиры основного металла недопустимы.
Для деталей подвески допустимы следующие величины износа: 3 мм для тяги 1 (рис. 20); 1 мм для валиков 2, втулки тяги 5, втулки поддона 6; 1,5 мм для серьги 3, верхней 4 и нижней 7 гаек. При большом износе детали заменяют новыми или восстанавливают в соответствии с правилами деповского ремонта, утвержденными ЦТ МПС.
Замену пружин производят в определенном порядке. Надбуксовые пружины тележки заменяют после подъемки кузова вагона. При этом сначала следует расшплинтовать и отвернуть гайки шпинтонов буксовых узлов одной колесной пары. Затем поднять раму тележки настолько, чтобы шпинтоны вышли из надбуксовых пружин. Снять неисправную пружину и заменить ее новой.
После этого опустить раму и произвести сборку тележки в обратном порядке, соблюдая при этом правильное расположение деталей буксового фрикционного гасителя (амортизатора).
Перед тем как завернуть гайки шпинтонов, необходимо убедиться в правильном положении пружинных шайб (рис. 21). Наружная кромка шайбы должна входить в выточку фланца корончатой гайки, внутренняя — упираться в кромку фрикционной втулки. Гайки шпинтонов следует завертывать до отказа (до выпрямления пружинных шайб).
Сменять пружины центрального подвешивания под вагоном рекомендуется в следующем порядке:
- расшплинтовать и отвернуть гайки предохранительных болтов;
- отвернуть болты М12, снять крышки и вынуть предохранительные болты;
- не вынимая шкворня, поднять вагон вместе с тележкой на высоту 150—200 мм;
- подложить под поддон со стороны неисправной пружины подкладку (деревянный брусок или другие приспособления);
- опустить вагон и освобожденные серьги, соединяющие валики подвесок с валиками поддона, снять;
- вновь поднять вагон вместе с тележкой до освобождения пружинных комплектов;
- заменить неисправную пружину.
Сборку пружин центрального подвешивания под вагоном следует производить в обратном порядке.
Пружины центрального подвешивания на выкаченных из-под вагонов тележках рекомендуется заменять при помощи струбцин (см. рис. 21) или пневмоприжимов. Струбциной или пневмоприжимом подтягивают поддон к раме, при этом освобождаются серьги подвесок. Смену пружин ведут в описанном выше порядке.
Подбор пружин тележек типа КВЗ-ЦНИИ следует производить так же, как для тележек моторных вагонов.
Пружины следует подбирать в зависимости от тары, веса брутто вагона и его развески по концам в строгом соответствии с технической документацией на тележку для определенного типа вагона.
Ревизия гидравлических гасителей. Эту работу необходимо производить при плановых ремонтах вагонов в депо через каждые 100—150 тыс. км пробега на большом периодическом ремонте, а контрольные прокачки на вагонах вручную — на каждом малом периодическом ремонте. При выявлении неисправностей гасителей во время контрольной прокачки следует произвести их ревизию. Гасители, имеющие неисправности (подтеки масла, Заклинивание штока поршня и пр.), также подвергают ревизии.
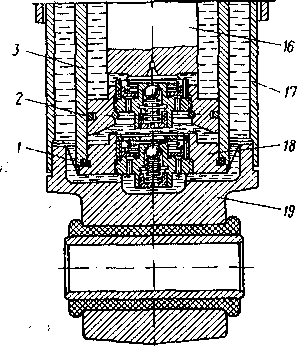
Рис. 22. Гидравлический гаситель тележки типа КВЗ-ЦНИИ: 1, 5 — кольца резиновые; 2 — кольцо поршневое; 3 — цилиндр; 4 — голов ка цилиндра; 6 — кольцо; 7 — гайка; 8 — штифт; 9 — головка верхняя; 10 – винт стопорный; 11 — гайка сальника; 12 — планка стопорная; 13 — сальник самоподжимиой ЛРТИ 72,5X47X10; 14 — корпус сальника; 15 — кожух верхний; 16 — шток; 17 — вспомогательный цилиндр; 18 — корпус нижнего клапана; 19 — головка нижняя
При обнаружении в депо на поверхности корпуса гидрогасителя масляной пленки без других следов течи масла из прибора необходимо прокачать гаситель колебаний под вагоном в следующем порядке:
- освободить верхнюю головку крепления прибора;
- гаситель повернуть в горизонтальное положение вокруг нижнего шарнира на себя;
- вручную ломиком, продетым в отверстие верхней головки крепления прибора, прокачать последний;
- количество ходов при прокачке должно быть 2—3.
Гаситель считается исправным, если поршень перемещается плавно, туго и без рывков.
При ревизии необходимо произвести полную разборку гасителя в следующем порядке:
- Отвернуть стопорный винт; зажать верхнюю головку гасителя в тисках в горизонтальном положении и отвернуть защитный кожух.
- Предварительно сняв стопорную планку, отвернуть гайку. Вынуть шток поршня вместе с рабочим цилиндром и корпусом сальника, а также стопорный штифт.
- Затем слить масло из цилиндров гасителя в чистую посуду.
- Легкими ударами по головке штока выбить нижний клапан и головку цилиндра, после чего вынуть из цилиндра шток поршня.
- Отвернуть верхнюю головку гасителя, зажав в тисках шток. (Губки тисков должны быть защищены прокладками из мягкого металла.)
- После этого снять корпус сальника и головку цилиндра.
Для выемки сальников необходимо отвернуть гайку специальным ключом. Сальники заменяют новыми при течи масла через уплотнение или при механических повреждениях (выкрашивание резины и т. д.). В гидравлическом гасителе тележки типа КВЗ-ЦНИИ (рис. 22) используют стандартные самоподжимные каркасные сальники (манжеты) марки ЛРТИ 72,5x47x10, применяемые в автотракторной промышленности.
Верхний и нижний кожухи гидрогасителя промывают в щелочном растворе, остальные детали, кроме резиновых, — в мыльной эмульсии, бензине или керосине.
После просушки проверяют соответствие размеров всех деталей. Изношенные и вышедшие из строя детали ремонтируют или заменяют новыми.
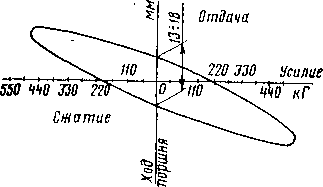
Рис. 23. Рабочая диаграмма гасителя
Затем гидрогаситель заправляют маслом. При этом применяют только приборное масло МВП ГОСТ 1805—51 в количестве 0,78 л; перед заправкой его необходимо профильтровать через металлическую сетку № 018 ГОСТ 6613—53. Масло заливают во вспомогательный цилиндр, закрепленный вертикально в тисках за нижнюю головку. В цилиндр вставляют рабочий цилиндр в сборе (со штоком, корпусом сальника и верхней головкой), гайку следует затянуть.
Остальные операции по сборке гидравлических гасителей производят в порядке, обратном порядку разборки.
Для заполнения рабочего цилиндра маслом и удаления из него воздуха собранный гидрогаситель предварительно прокачивают вручную, продев ломик в отверстие верхней головки. После этого его устанавливают на испытательный стенд для прокачки в течение 2 мин. С целью визуальной проверки качества уплотнения верхний кожух гидрогасителя снимают. Течь масла через сальник при прокачке недопустима.
Все гасители, проходящие ревизию, в сроки, оговоренные выше, необходимо испытать на стенде (при испытаниях ход ползуна должен быть равен 40±3 мм, а частота — 60 ходов в 1 мин.) для проверки их работоспособности. Стенд должен иметь приспособление для записи рабочей диаграммы «усилие—перемещение» на специальный бланк. Усилие на штоке, замеренное по диаграмме (ход поршня гасителя при снятии диаграммы должен быть равен 13—18 мм, температура рабочей жидкости 15—25°С, рис. 23), должно быть: при ходе вверх 550±50100 кГ, а при ходе вниз — 50±50100 кГ.
После испытания гидрогасителей проверяют сальниковое уплотнение, для этого их держат в горизонтальном положении в течение 12 ч.
Гидрогасители испытывают в присутствии мастера цеха и приемщика МПС. Принятые гидрогасители должны иметь на видимой поверхности нижней головки четко нанесенные набивные клейма с указанием месяца и года ревизии, а также номера депо, проводившего ревизию.
Проверочно-регулировочные работы. Эти работы выполняют на всех вновь собранных тележках при подкатке их под вагон. Проверяют, соответствуют ли тележки техническим требованиям, и, если имеются отклонения, производят необходимые регулировочные работы.
Проверку и соответствующие регулировочные работы рекомендуется производить в приведенной ниже последовательности.
- Проверить и отрегулировать зазор между пятником и подпятником вагона. Этот зазор контролируют, замеряя зазор а (см. рис. 18), который должен быть в пределах 16^1 мм. В случае отклонения зазора а от этой величины следует его установить, подкладывая регулировочные прокладки под съемные скользуны тележек. Скользун ДСП-Г должен быть опущен в коробку не менее чем на 17 мм.
- Отрегулировать высоту оси автосцепки относительно головок рельсов. Регулировку производят в случае несоответствия этого размера величине, установленной правилами технической эксплуатации. При этом используют регулировочные прокладки (см. рис. 17), которые ставят обязательно под все опорные подшипники люлечных подвесок одной стороны тележки. Под каждый подшипник разрешается устанавливать не более двух прокладок, общая толщина которых не превышает 20 мм. Регулировочные прокладки толщиной до 15 мм можно ставить под пружинные комплекты центрального подвешивания (см. рис. 18). Под буксовые пружины устанавливают прокладки общей толщиной не более 8 мм. Регулировочные, прокладки под пружинами буксового и центрального подвешивания с одной стороны тележки должны быть одинаковой толщины.
- Проверить, правильно ли установлены предохранительные стержни после проверки высоты автосцепки на вагоне.
При установке предохранительных стержней 8 (см. рис. 18) необходимо следить за тем, чтобы после закрепления гаек 6 шплинтами оставался зазор от 1 до 2 мм между набором опорных шайб и сферой дна поддона. Для этого гайки предохрайительных стержней завертывают до тех пор, пока (без натяжения) опорные шайбы не коснутся дна поддона. Затем гайки отвертывают (на полоборота) и зашплинтовывают.
В случае установки регулировочных подкладок под опорные подшипники подвесок (см. п. 2) необходимо ставить под головку стержня регулировочные прокладки 10 такой же толщины. Регулировку положения надрессорного бруса и гидрогасителей производить при помощи поводков запрещается. - Установить продольные поводки (тяги 17) под тарой вагона. Правильная установка поводков должна обеспечить расчетную затяжку резиновых пакетов при одновременном соблюдении симметричного (по отношению к раме тележки) расположения надрессорного бруса и гидрогасителей.
Затяжку пакетов производить до исчезновения вогнутости резины по Периметру. (Разрешается местная или кольцевая выпуклость резины на величину до 3 мм.) При затяжке должно быть обеспечено одновременное сжатие двух пакетов с соблюдением правильного взаимного расположения резиновых пакетов и фланцев. При затяжке гаек должно быть обеспечено правильное взаимное расположение резиновых пакетов и фланцев. - Проверить положение надрессорного бруса и гидрогасителей. Это производят после регулировки поводков5. Цель регулировки положения надрессорного бруса — обеспечить необходимые зазоры вид (см. рис. 18). Зазор в должен быть не менее 5 мм, зазор д — не менее 35 мм, а суммарный зазор 2 д — в пределах 85+5 мм. Зазоры вид регулируют путем подбора по толщине накладок, привариваемых на продольных балках рамы тележек и скользунах поперечных балок. Зазор должен быть не менее 7 мм. При установке гидрогасителей необходимо располагать их симметрично на кронштейнах надрессорного бруса. Эту регулировку можно производить путем перестановки резиновых шайб 15.
- Отрегулировать положение предохранительных скоб надрессорного бруса. При регулировке 6 необходимо оставить зазор к (под тарой) не менее 140+10 мм, для чего надо поставить шайбы 3. Разрешается переставлять шайбы 3 сверху вниз и обратно.
При подкатке тележек под вагон следует обращать внимание на состояние опорных поверхностей горизонтальных скользунов 22 (см. рис. 18). Эти поверхности должны быть тщательно очищены от грязи и продуктов коррозии.