В механическую часть электропоезда входят: кузов вагона со сцепными приборами, тележки с колесными парами, рессорным подвешиванием, тяговой зубчатой и рычажной тормозной передачами. Кузов является цельнометаллической несущей конструкцией, которая воспринимает все нагрузки, действующие на вагон. В нем размещены пассажирские помещения с диванами для пассажиров и другое оборудование, а также кабины управления и шкафы с электрической аппаратурой. Под кузовом находятся силовая аппаратура, вспомогательные машины, тормозное оборудование.
Кузов опирается на тележки и шарнирно с ними связан через шкворневое устройство.
Тележки имеют двойное рессорное подвешивание с фрикционными гасителями колебаний в буксовом подвешивании и гидравлическими амортизаторами (демпферами) в центральном подвешивании. От тележек на раму кузова передаются тяговые и тормозные усилия. Тележки обеспечивают плавность хода вагона за счет гашения вертикальных и горизонтальных колебаний при движении по неровностям пути. При прохождении кривых участков пути тележки поворачиваются в горизонтальной плоскости относительно вагона, и колесные пары устанавливаются по радиусу кривой. Это уменьшает набегание колес на рельс, а значит снижает износ колес, обеспечивая нормальное вписывание в кривую.
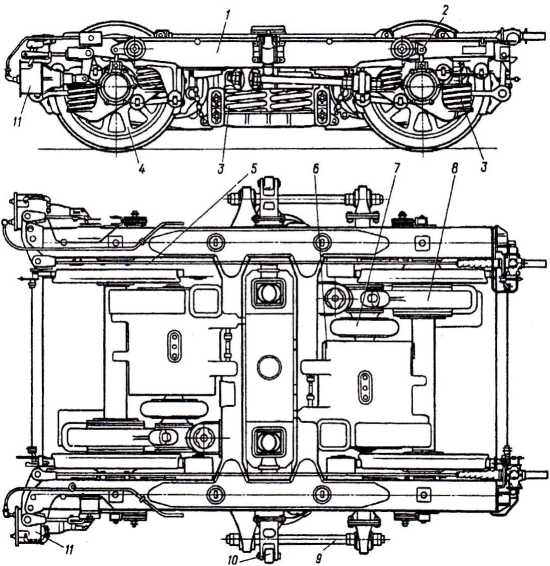
Рис. 1.32. Тележка моторного вагона электропоезда ЭР2Т: 1 —рама; 2— фрикционный гаситель; 3— пружины рессорного подвешивания; 4— колесные пары с буксовыми узлами; 5— рычажно-тормозная передача; 6 — тяговый двигатель; 7— упругая муфта; 8 — редуктор; 9— буксовый поводок; 10 — гидравлический гаситель; 11 — тормозной цилиндр
К поперечным балкам тележек моторных вагонов жестко подвешены тяговые двигатели и одной стороной шарнирно присоединены корпуса редукторов зубчатой передачи. Другой стороной корпус редуктора опирается на ось колесной пары. В центральном рессорном подвешивании установлены четыре комплекта двухрядных цилиндрических пружин и гидравлические амортизаторы (демпферы).
Включение и выключение печей производится контакторами, которыми управляет терморегулятор. При нормальной работе термоавтоматики в салоне должна поддерживаться температура + 16 °C при окружающей температуре до – 30°C и +11 °C при внешней температуре – 35°C.
Охлаждение тяговых двигателей и преобразователей. Тяговые двигатели и преобразователи охлаждаются с помощью самовентиляции. Для этого на вал якоря двигателя насажен вентилятор, который через жалюзи 8, сетку фильтра и подвагонный канал засасывает воздух. Входной патрубок тягового двигателя соединен с подвагонным каналом гибким соединением 7. Жалюзи и фильтры расположены на обеих боковых стенах кузова вагона, поэтому каждый двигатель, имеет свой фильтр. Во время движения поезда воздух засасывается вентилятором через жалюзи, очищается и по подвагонному каналу подается на охлаждение в тяговый двигатель.
Для отвода тепла от преобразователей в нижней части боковых стен на прицепных вагонах также имеются жалюзи и камеры с фильтрами, которые соединяются с преобразователями гибкими патрубками. Наружный воздух засасывается вентилятором преобразователя через жалюзи, очищается в фильтровой камере и поступает к лопаткам вентилятора. После охлаждения преобразователя воздух выбрасывается наружу.
Тележки прицепных вагонов — бесчелюстные; надрессорный люлечный брус, как и на тележках моторных вагонов, фиксируется относительно поперечных балок тележки двумя горизонтальными поводками вместо применяемых ранее вертикальных скользунов. Кузов вагона опирается через боковые скользуны на надрессорный люлечный брус тележки. Тяговые и тормозные усилия передаются от колесных пар на кузов не только через горизонтальные поводки, но и через центральный шкворень, шарнирно соединяющий тележку с рамой кузова.

Рис. 1.33. Передняя тележка головного вагона: 1 — колесная пара; 2 — пружины центрального рессорного подвешивания; 3 — привод скоростемера; 4 — пружина буксового подвешивания; 5 — приемная катушка АЛСН; 6— рама; 7— рычажно-тормозная передача; 8 — авторегулятор; 9—тарель; 10—контролируемый зазор 16+2 (-4) пятникового устройства
Общий вид тележки моторного вагона электропоездов ЭР2Т и ЭД2Т показан на рис. 1.32, тележки прицепного вагона — на рис. 1.33.
Рамы тележек. Рамы тележек моторных вагонов электропоездов ЭР2 (рис. 1.34) — челюстного типа. В горизонтальной плоскости они имеют Н-образную форму. Рама состоит из двух продольных балок 11 и соединяющих их двух средних поперечных балок 6. Продольные балки сваривают из двух штампованных профилей швеллерообразного сечения с толщиной стенки 12 мм. Стыки продольных балок с поперечными усиливают сверху и снизу фасонными накладками 13 из стального листа толщиной 14 мм. К продольным балками приварены кронштейны для крепления тормозных цилиндров, деталей рычажной передачи, центрального рессорного подвешивания, гидравлических и фрикционных гасителей, буксовые направляющие 3, 8.
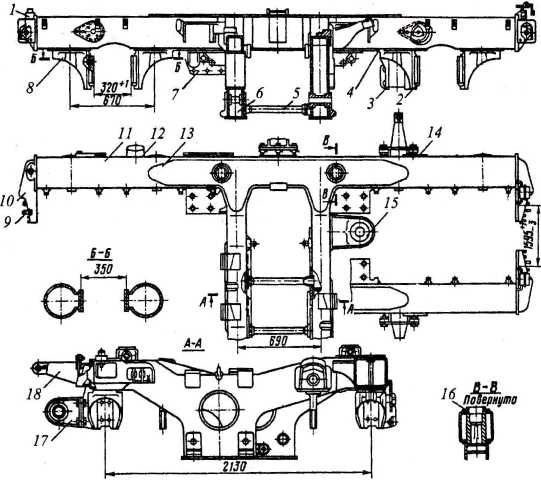
Рис. 1.34. Рама тележки моторного вагона электропоезда ЭР2: 1 — кронштейн оси горизонтального тормозного рычага; 2 — буксовый наличник; 3, 8— буксовые направляющие; 4 — усиливающая накладка; 5 — распорка; б — поперечная балка; 7 — плита тормозного цилиндра; 9 — кронштейн подвески тормозной траверсы; 10 — концевая балка; 11 — продольная балка; 12 — кронштейн наклонного тормозного рычага; 13 — верхняя усиливающая накладка; 14 — основание фрикционного гасителя колебаний; 15— кронштейн подвески редуктора; 16-— стальная гильза; 17 — кронштейн горизонтального поводка; 18 — кронштейн гидравлического гасителя колебаний
В средней их части (напротив поперечных балок) вварены стальные литые гильзы, через которые пропущены подвески центрального рессорного подвешивания. Поперечная балка имеет сложную конфигурацию потому, что к ней крепится тяговый двигатель и подвешивается редуктор. Балку сваривают из двух штампованных элементов толщиной 10 мм. К ее нижней части приварены литые опоры для крепления тягового двигателя. Сверху имеются упоры для клиньев, которыми двигатель притягивается к тележке. С правой стороны от упоров приварен кронштейн для подвески редуктора. Внизу между обеими поперечными балками установлены две расраспорки 5, которые придают конструкции необходимую жесткость. Материалом для изготовления деталей рамы является малоуглеродистая сталь марки Ст3.
Рамы тележки моторных вагонов электропоездов ЭР2Т и ЭД2Т в основном аналогичны описанным. Они также состоят из двух продольных и двух поперечных балок. На продольных балках отсутствуют буксовые направляющие, вместо них к балкам приварены стальные литые кронштейны 3 для крепления поводков (рис. 1.35), фиксирующих буксу.
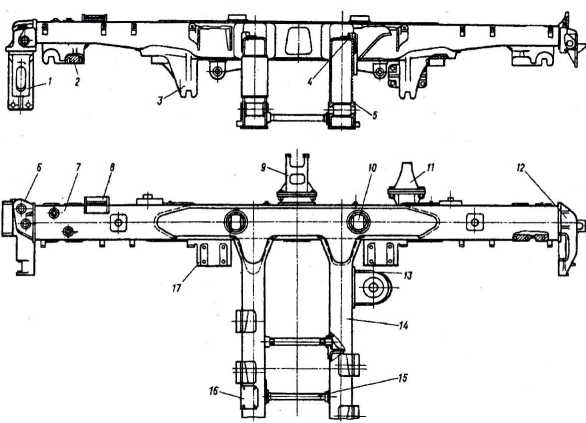
Рис. 1.35. Рама тележки моторного вагона электропоездов ЭР2Т, ЭД2Т: 1, 6, 8, 17— кронштейны рычажно-тормозной передачи; 2— кронштейн буксовых пружин; 3— кронштейн буксовых поводков; 4, 5— опоры крепления тяговых двигателей; 7 — продольные балки; 9 — кронштейн гидравлического гасителя; 10 — трубы центрального подвешивания; 11 — кронштейн тяговых поводков; 12 — концевые балки; 13 — кронштейн подвески редуктора; 14 — поперечная балка; 15— распорка; 16— кронштейн для авторежима
Рамы тележек прицепных вагонов штампосварной конструкции также имеют Н-образную форму. Продольные балки сварены из двух швеллеров и усилены сверху и снизу накладками из листовой стали толщиной 14 мм. К концам продольных балок приварены фигурные фланцы, к каждому из которых четырьмя болтами прикреплены шпинтопы, центрирующие положение пружин буксового рессорного подвешивания. К продольным балкам, как и на моторных вагонах, приварены кронштейны для гидравлических гасителей и кронштейны для присоединения продольных поводков. Поперечные балки имеют коробчатое сечение и свариваются из листовой стали.
К раме первой тележки головного вагона прикреплен горизонтальный брус из швеллера. При помощи угольников и косынок к нему подвешены приемные катушки автоматической локомотивной сигнализации. Там же установлена коробка зажимов для соединения проводов. Провода проложены в трубах (кондуитах). Брус вместе с приемными катушками предохраняется от падения на путь стальными тросами.
Рессорное подвешивание. Рессорное подвешивание обеспечивает необходимую упругость при передаче веса вагона на тележку, оно служит для амортизации и частичного гашения колебаний как вертикальных, так и горизонтальных, возвращает кузов вагона в нормальное положение после выхода из кривой.
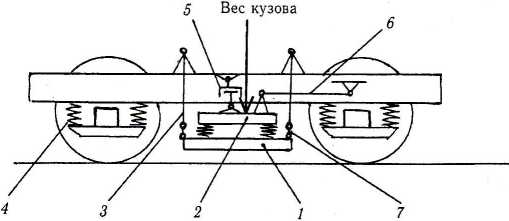
Рис. 1.36. Схема двойного рессорного подвешивания: 1 — поддон; 2 — надрессорный брус; 3 — подвеска; 4 — пружина; 5 — гидравлический гаситель; 6 — поводок; 7 — серьга
Раньше на тележках применяли тройное рессорное подвешивание, сейчас — двойное. Оно состоит из двух ступеней, которые работают последовательно: надбуксовое подвешивание, расположенное в буксовом узле, и центральное люлечное подвешивание, размещенное в центре тележки. Схема двойного подвешивания приведена на рис. 1.36. Если на электросекциях первых выпусков рессорное подвешивание в основном составлялось из листовых рессор различной конфигурации, то теперь перешли на цилиндрические пружины, что потребовало установки амортизаторов (гидравлических, фрикционных и т.п.). Листовые рессоры имели значительное внутреннее трение между листами и высокочастотные колебания гасить не могли. Они проявлялись в виде вибрации, шума. Цилиндрические рессоры не имеют внутреннего трения и обеспечивают плавный и бесшумный ход вагона.
На неподвижном вагоне пружины рессор испытывают только статическую нагрузку от массы кузова. При движении по неровностям пути кузов совершает вертикальные колебания, поэтому нагрузка на пружины существенно изменяется. Величину, на которую она увеличивается или уменьшается, называют динамической нагрузкой. Суммируя статическую и динамическую нагрузки, рассчитывают прочность пружин, по разности этих нагрузок определяют минимальное давление колесной пары на путь, чтобы исключить возможность схода с рельсов, т.е. обеспечить безопасное качение колесной пары.
В буксовом узле расположена первая ступень подвешивания, которая смягчает удары, воспринимаемые колесной парой. Эта же ступень подвешивания одновременно снижает нагрузки, передаваемые от кузова через центральное подвешивание на колесную пару.
Надбуксовое рессорное подвешивание поездов ЭР2Т и ЭД2Т состоит из двух комплектов цилиндрических пружин. Корпус буксы моторного вагона имеет ступенчатое расположение крыльев под установку рессор (одно крыло выше, другое ниже — для лучшей фиксации корпуса буксы). Два поводка 3 и 5 закреплены в двух приливах (рис. 1.37) — верхнем и нижнем. Один конец поводка с помощью валика соединен с кронштейном рамы, другой — с приливом буксы. Кронштейны и приливы имеют клиновидные пазы, в которые входят головки валиков поводков, закрепляемые болтами.
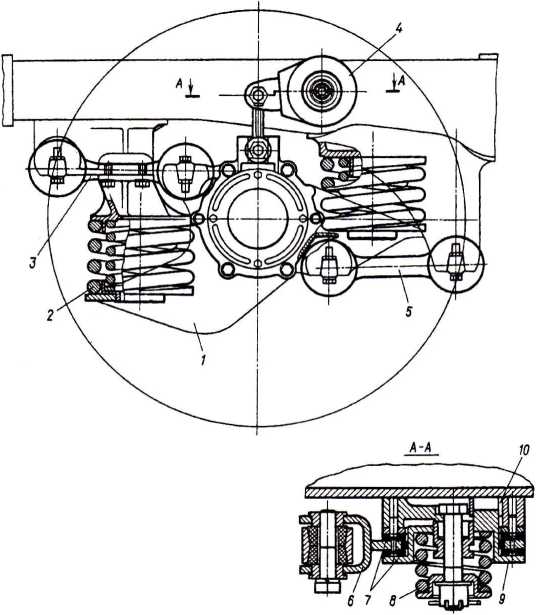
Рис. 1.37. Надбуксовое рессорное подвешивание тележки моторного вагона электропоезда ЭР2Т: 1 — корпус буксы; 2— комплект пружин; 3, 5 — поводки для передачи продольных усилий; 4 — фрикционный гаситель; 6 — рычаг; 7 — фрикционные диски; 8 — пружина; 9 — стакан; 10 — втулка
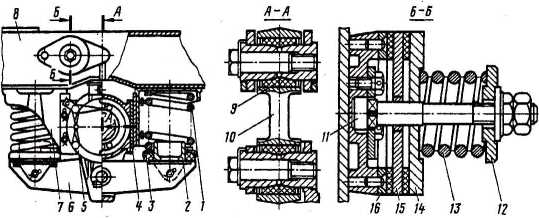
Рис. 1.38. Надбуксовое рессорное подвешивание тележки моторного вагона электропоезда ЭР2: 1 — пружина; 2 — стакан; 3 — резиновый амортизатор; 4 — наличники; 5 — букса; 6 — балансир; 7 — буксовая направляющая; 8 — продольная балка рамы тележки; 9 — резиновая втулка; 10 — поводок фрикционного гасителя; 11 — ось; 12 — фигурная шайба; 13 — пружина; 14 — крышка; 15—поворотный рычаг с фрикционными дисками; 16 — неподвижный диск
Поводки насажены на валики с натягом и при помощи резинометаллических втулок ограничивают разбег колесной пары в продольном направлении до 1 мм, в поперечном — до 7,5 мм. На опорных поверхностях буксы расположены резиновые амортизаторы, армированные стальными стаканами. На верхние части пружин опирается рама, для чего на ней имеются опорные стаканы.
Корпус буксы моторного вагона и продольную раму тележки соединяет фрикционный гаситель 4 (см. рис. 1.37), который поглощает вертикальные колебания тележки. Его ось закреплена на основании, которое приварено к раме тележки. На оси расположен поворотный рычаг 6, армированный с обеих сторон фрикционными дисками (пластмасса, гетинакс). Рычаг зажат пружиной (ее усилие регулируют гайкой) и шарнирно связан поводком с крышкой буксы. В местах соединения поводка установлены резиновые втулки, допускающие перекос поводка. Они гасят мелкие колебания, при больших амплитудах подключается фрикционная часть гасителя. Гашение колебаний происходит за счет трения в паре “гетинакс—сталь”, так как фрикционные диски прижаты друг к другу пружиной 8.
Корпус буксы моторного вагона электропоезда ЭР2 стальной, литой. В нижней части он имеет хвостовик в виде хомута (рис. 1.38). Через хвостовик проходит стальной балансир 6 с укрепленными на его концах опорными стаканами 2. Стаканы закреплены болтами и служат для установки цилиндрических буксовых пружин 1. Балансир соединен с хвостовиком буксы стальным валиком. Чтобы уменьшить износ, между валиком и хвостовиком запрессованы сменные цементированные стальные втулки.
Цилиндрические пружины опираются на стаканы 2, под пружинами расположены резиновые амортизаторы 3. которые устраняют контакт между ними и опорными стаканами балансира. Для предотвращения износа резины от контакта с торцом пружины уложено металлическое кольцо. На верхние концы пружин опирается рама тележки, для этого в буксовых направляющих сделаны “чашки”.
На корпусе буксы имеются наличники 4, на которых взаимно перпендикулярно расположены большие и малые пластины. Большие пластины ограничивают разбег колесной пары вдоль тележки, малые — в поперечном направлении. Между наличниками буксы и наличниками буксовых направляющих рамы тележки имеются зазоры: вдоль оси колесной пары — 2.. .4 мм, поперек оси — 1.. .3 мм (в сумме на обе стороны). В эксплуатации допускаются наибольшие поперечные зазоры 5 мм, продольные — 7 мм. Для гашения вертикальных колебаний (так же, как и на электропоездах ЭР2Т) в верхней части крышки буксы имеется прилив для крепления фрикционного гасителя.
Буксовое подвешивание прицепных вагонов несколько отличается от подвешивания моторных. К опорным плитам на концах продольных балок прикреплены болтами стальные литые шпинтоны 1 (рис. 1.39), которые служат направляющими для буксовых пружин 2. На пружины опирается рама тележки, нижние части пружин лежат на стальных прокладках 4и резиновых амортизаторах 6. Стальные прокладки предохраняют резину от износа.
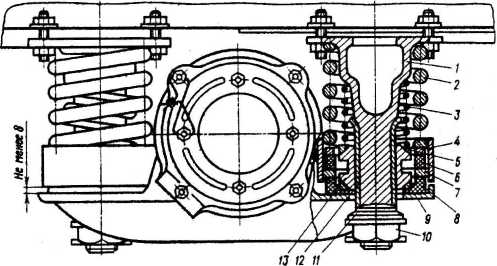
Рис. 1.39. Надбуксовое рессорное подвешивание тележки прицепного вагона: 1 — шпинтон; 2— пружина; 3 — внутренняя пружина; 4— стальная прокладка; 5, 9— конические кольца; 6. 8— резиновые гасители; 7— подкладка нижнего гасителя; 10 — гайка; 11 — пружинная шайба; 12 — гильза; 13 — сухарь
таком положении удерживается шкворнем. Шкворень состоит из трех частей: двух полушкворней с буртиками и клина, который раздвигает и закрепляет полушкворни. От падения полушкворни удерживаются своими буртиками в шкворневом гнезде. Плоские пятники просты в изготовлении, имеют большую площадь опоры и меньшее трение при повороте тележки относительно кузова, но требуют регулярного смазывания и тщательного ухода.
Гидравлический гаситель колебаний. При использовании цилиндрических пружин в рессорном подвешивании обязательно наличие гасителей колебаний. Одним концом гаситель прикреплен к кронштейну надрессорного бруса, другим — к кронштейну, приваренному к продольной балке тележки. Он имеет цилиндрическую форму и состоит из двух частей, которые перемещаются относительно друг друга в осевом направлении.
Верхняя часть гасителя состоит из верхней головки 2 (рис. 1.42), штока 9, оканчивающегося поршнем, защитного кожуха 8, который предохраняет внутреннее устройство аппарата от попадания грязи и влаги. Поршень уплотнен поршневым кольцом 14.
Нижняя часть гасителя состоит из нижней головки 12, запасного резервуара 10 и рабочего цилиндра 16. В запасной резервуар, как и в рабочий цилиндр, заливается приборное масло МВП. К верхней части запасного резервуара (вспомогательного цилиндра) присоединен корпус, в который вставлены сальники 6 (манжеты).
В верхнюю часть рабочего цилиндра с резиновым уплотнительным кольцом запрессована головка рабочего цилиндра, она же является направляющей для штока 9 гасителя. Корпус сальника 7 через уплотнительное резиновое кольцо 18 и металлическое кольцо 19 закреплен гайкой 20 в запасном резервуаре. Основание корпуса сальника упирается в верхнюю поверхность направляющей штока. В нижнюю часть рабочего цилиндра запрессован корпус нижнего клапана, который опирается на внутреннюю поверхность нижней головки 12.
Гашение колебаний вагона происходит благодаря вязкому трению масла, возникающему при продавливании его поршнем через узкие дроссельные каналы и всасыванию обратно через рабочий клапан одностороннего действия.
Резиновые амортизаторы уложены в чашках крыльев буксы и закрыты опорными кольцами 7. Нижние концы шпинтонов 1 проходят через отверстия в крыльях буксы и оканчиваются резьбой, на которую навертывается корончатая гайка 10. На гайке лежит тарельчатая пружина И, упирающаяся в торец втулки 12, напрессованной на шпинтон. При движении втулка смягчает удары гайки шпинтона о крыло буксы.
Буксовое подвешивание дополнено фрикционным (клиновым) амортизатором. Его конструкция довольно проста, и он не требует ухода в эксплуатации. Трение в амортизаторе создают шесть сухарей 13, расположенных по окружности втулки шпинтона. Сухари находятся между двумя стальными коническими кольцами 5 и 9. Верхнее кольцо постоянно прижимается сверху пружиной 3, которая упирается в утолщенную часть шпинтона. Нижнее кольцо опирается на резиновый амортизатор 8. Благодаря двойному конусу сухарей и колец пружина 3создает усилие, прижимающее сухари 13 к втулке 12. При взаимодействии сухарей и втулки, с усилием прижатых друг к другу, возникают силы трения, уменьшающие колебания в буксовом узле.
Центральное рессорное подвешивание моторных и прицепных вагонов сходно по конструкции, принцип его действия одинаковый. Центральное подвешивание представляет собой шарнирную систему (люльку), состоящую из поддона 16 (рис. 1.40), который при помощи серег 13 и подвесок 1 связан с продольной балкой тележки. Через комплект пружин на поддоны опирается надрессорный люлечный брус. На его верхней части установлены шкворневое устройство и скользуны 4. воспринимающие вес кузова вагона.
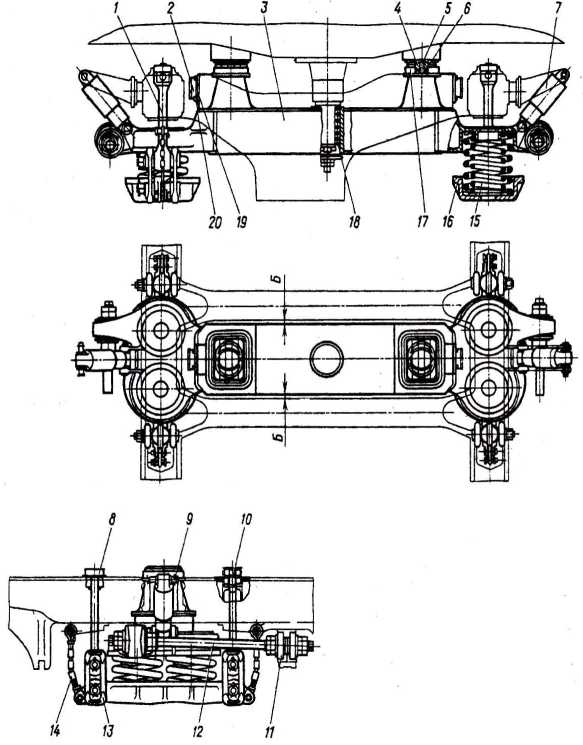
Рис. 1.40. Центральное рессорное подвешивание тележки моторного вагона электропоезда ЭР2Т: 1 — подвеска; 2 — амортизатор для ограничения поперечных перемещений надрессорного бруса; 3 — надрессорный брус; 4 — скользун; 5 — прокладка; 6 — резиновая прокладка; 7 — гидравлический гаситель; 8 — колпачок; 9, 10 — валики; 11 — амортизатор; 12 — поводок; 13 — серьга; 14 — предохранительный трос; 15 — пружина; 16—поддон; 17 — коробка скользуна; 18 — шкворень с гасителем; 19, 20 — прокладки
Таким образом, поддоны связаны с продольными балками рамы тележки двойной шарнирной системой —- длинными подвесками и короткими серьгами. Из-за наклона кузова во время движения вагона по кривой подвески поворачиваются на определенный угол. При этом на поддон действует сила, которая стремится возвратить вагон в исходное нормальное положение. Она передается через подвески на раму тележки, и чем больше угол наклона подвески, тем больше возвращающая сила. При больших отклонениях кузова подтаком положении удерживается шкворнем. Шкворень состоит из трех частей: двух полушкворней с буртиками и клина, который раздвигает и закрепляет полушкворни. От падения полушкворни удерживаются своими буртиками в шкворневом гнезде. Плоские пятники просты в изготовлении, имеют большую площадь опоры и меньшее трение при повороте тележки относительно кузова, но требуют регулярного смазывания и тщательного ухода.
Гидравлический гаситель колебаний. При использовании цилиндрических пружин в рессорном подвешивании обязательно наличие гасителей колебаний. Одним концом гаситель прикреплен к кронштейну надрессорного бруса, другим — к кронштейну, приваренному к продольной балке тележки. Он имеет цилиндрическую форму и состоит из двух частей, которые перемещаются относительно друг друга в осевом направлении.
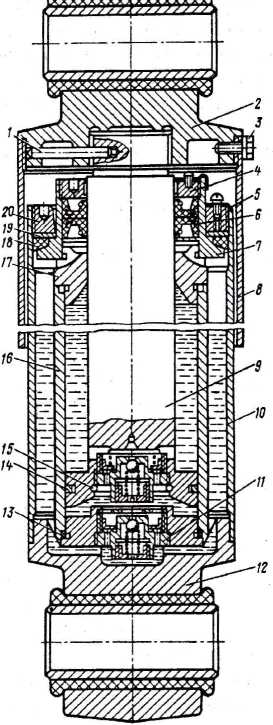
Рис. 1.42. Гидравлический гаситель: 1 — штифт; 2— верхняя головка; 3— стопорный винт; 4— гайка сальника; 5— стопорная планка; 6— сальник; 7— корпус сальника; 8— защитный кожух; 9— шток; 10— запасной резервуар; 11 — нижний клапан; 12— нижняя головка; 13, 18— резиновые кольца; 14 — поршневое кольцо; 15— стопорное кольцо; 16— рабочий цилиндр; 17— головка рабочего цилиндра; 19— металлическое кольцо; 20 — гайка
Верхняя часть гасителя состоит из верхней головки 2 (рис. 1.42), штока 9, оканчивающегося поршнем, защитного кожуха 8, который предохраняет внутреннее устройство аппарата от попадания грязи и влаги. Поршень уплотнен поршневым кольцом 14.
Нижняя часть гасителя состоит из нижней головки 12, запасного резервуара 10 и рабочего цилиндра 16. В запасной резервуар, как и в рабочий цилиндр, заливается приборное масло МВП. К верхней части запасного резервуара (вспомогательного цилиндра) присоединен корпус, в который вставлены сальники 6 (манжеты).
В верхнюю часть рабочего цилиндра с резиновым уплотнительным кольцом запрессована головка рабочего цилиндра, она же является направляющей для штока 9 гасителя. Корпус сальника 7 через уплотнительное резиновое кольцо 18 и металлическое кольцо 19 закреплен гайкой 20 в запасном резервуаре. Основание корпуса сальника упирается в верхнюю поверхность направляющей штока. В нижнюю часть рабочего цилиндра запрессован корпус нижнего клапана, который опирается на внутреннюю поверхность нижней головки 12.
Гашение колебаний вагона происходит благодаря вязкому трению масла, возникающему при продавливании его поршнем через узкие дроссельные каналы и всасыванию обратно через рабочий клапан одностороннего действия.
Поршень может перемещаться вверх-вниз в рабочем цилиндре, наполненном маслом, в зависимости от колебаний тележки. Во внутреннюю полость поршня ввернут верхний двойной клапан, аналогичный клапан имеется и в нижней крышке рабочего цилиндра. При движении поршня вниз (ход сжатия) верхний клапан приподнимается, и масло из-под поршневой полости свободно перетекает в надпоршневую полость. В то же время шток 9. входя в рабочий цилиндр, стремится вытеснить масло и часть его перетекает через дроссельное отверстие нижнего клапана в запасной резервуар. В случае резкого хода поршня вниз давление над ним также резко повышается. Когда оно станет равным примерно 4,5 МПа, откроется шариковый клапан нижнего клапанного устройства.
При движении поршня вверх (ход растяжения) верхний клапан закрывается, давление масла в надпоршневой полости повышается, и часть масла перетекает через дроссельные отверстия верхнего клапана в подпоршневую полость. Затем приподнимается нижний клапан, и часть масла засасывается из запасного резервуара.
При плавном ходе поршня вверх масло находится под высоким давлением только над поршнем. В случае резкого движения штока или загустевания масла при низких температурах давление в полости над поршнем резко повышается, так как масло не успевает перетечь через дроссельное отверстие клапана. Когда давление достигает примерно 4,5…5,0 МПа, открывается шариковый клапан.
Шариковые клапаны (верхнего и нижнего клапанов) являются разгрузочными. Они предназначены для ограничения сопротивления гасителя при больших скоростях перемещения поршня или повышении вязкости масла при низких температурах окружающего воздуха. Этот клапан представляет собой шарик, прижимаемый цилиндрической пружиной. Когда давление масла в рабочем цилиндре превысит определенную величину (4,5 МПа), клапан сработает и пропустит часть масла в обход дроссельного отверстия. Рабочий ход поршня гидравлического гасителя составляет 190 мм.
Буксовый узел. Буксы служат для соединения колесных пар с тележками и передачи нагрузки от веса вагона на шейки осей колесных пар. Буксы также воспринимают тяговые и тормозные усилия от колесных пар и передают их на раму тележки. Кроме того, корпус буксы защищает шейку оси и подшипники от влаги и грязи. Он заполнен смазкой ЖРО. необходимой для нормальной работы подшипников.
В буксовом узле расположена первая ступень рессорного подвешивания, смягчающая удары колесной пары. Букса состоит из стального литого корпуса, крышек, лабиринтных колец, подшипников и деталей, связывающих ее с рамой тележки. Внутренняя полость корпуса имеет цилиндрическую поверхность под посадку подшипников.
Подшипники содержат внутренние и наружные кольца, между которыми в сепараторе находятся ролики. Внутренние кольца подшипников устанавливают на шейку оси с натягом в горячем состоянии, наружные — свободно. Диаметр шейки оси и размеры подшипников определяются нагрузкой и допустимой частотой вращения (диаметр шейки оси 130 мм, длина ролика 80 мм).
Монтаж буксы колесной пары моторного вагона. На предподступичную часть оси (рис. 1.43) в горячем состоянии напрессовывают лабиринтное кольцо 14, внутреннее кольцо подшипника 12 с задним упорным буртиком. Затем на шейку оси надевают внутреннее дистанционное кольцо 2 и внутреннее кольцо подшипника 10. После этого устанавливают корпус буксы 11 с ранее вставленными в него наружными кольцами, сепараторами с роликами.
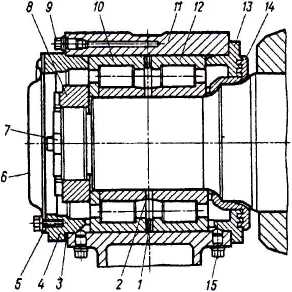
Рис. 1.43. Букса моторного вагона электропоездов ЭР2Т, ЭД2Т: 1, 2 — большое и малое дистанционные кольца; 3 — уплотнительное кольцо; 4 — крышка; 5— прокладка; 6 — смотровая крышка; 7— стопорная планка; 8 — торцевая гайка; 9, 15—пробки; 10. 12—подшипники; 11 —корпус буксы; 13— задняя крышка; 14 — лабиринтное кольцо
Детали, напрессованные на ось колесной пары, стягивают мощной торцовой гайкой 8, которую фиксируют стопорной планкой 7. Планка укреплена на торце оси двумя болтами. Снаружи букса закрыта смотровой крышкой 6и крышкой 4, имеющей кронштейн для поводка фрикционного амортизатора (гасителя). Со стороны колеса букса уплотнена лабиринтами, расположенными в кольце 14 и самом корпусе. На задней стенке, как и на передней, имеется крышка 13. Лабиринтная часть корпуса буксы имеет очертание лабиринтного кольца и глубокие канавки, не позволяющие вытекать смазке.
Таким образом, наружные кольца подшипников зафиксированы крышками 4и 13, внутренние кольца—торцевой гайкой 8 и лабиринтным кольцом (воротником) 14. В верхней части стенки корпуса буксы имеется отверстие, а в дистанционном кольце 1 — кольцевая канавка и восемь радиальных отверстий, через которые к подшипникам подается консистентная смазка. Отработанная смазка удаляется через два отверстия в нижней части корпуса. Отверстия заглушены пробками 9 и 15. На рис. 1.44 показана букса моторного вагона ЭР2.
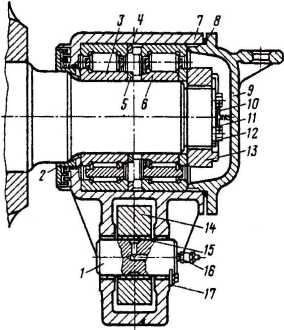
Рис. 1.44. Букса моторного вагона электропоезда ЭР2: 1 — валик балансира; 2— лабиринтное кольцо; 3— подшипник; 4— большое и малое дистанционные кольца; 7— корпус буксы; 8— уплотнительное кольцо; 9—крышка; 10—проволока; 11 — стопорная планка; 12—болт; 13 — торцовая гайка; 14— балансир; 15— втулка; 16— масленка; 17— стопорная пластина
Для соединения силовой цепи тяговых двигателей и высоковольтной схемы вспомогательных машин с “землей” служат заземляющие устройства. Они смонтированы на всех четырех крышках букс моторного вагона и электрически соединены между собой (т.е. работают параллельно). Эти устройства создают цепи для протекания тяговых токов в рельсы через колеса и оси колесных пар, минуя буксовые подшипники. Благодаря этому подшипники защищены от электроэрозии.
Заземляющее устройство представляет собой алюминиевый корпус 8 (рис. 1.45), внутри которого находится пластмассовый щеткодержатель 3. Корпус соединен с крышкой буксы шестью болтами, щетки 7 прижаты к токосъемному диску 11 пружинами. Диск устанавливают в проточке лабиринтного кольца 12 и закрепляют четырьмя болтами. Кольцо крепится к оси двумя болтами. Лабиринтное уплотнение, образованное кольцевыми канавками, защищает щетки от смазки, которая может попадать из полости буксы. Крышка заземляющего устройства имеет резиновую прокладку, предохраняющую механизм от пыли и грязи. Она плотно прижата к корпусу двумя откидными болтами.
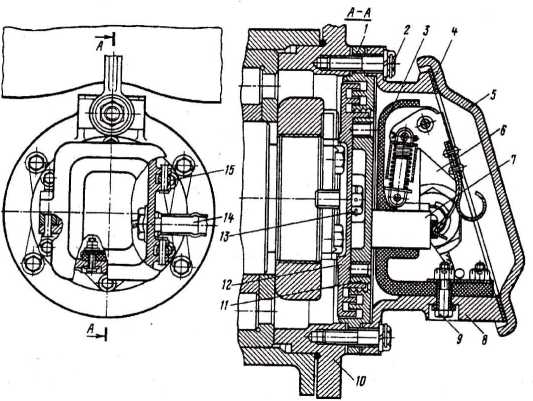
Рис. 1.45. Заземляющее устройство: 1 — лабиринтная крышка; 2, 13 — болты; 3 — щеткодержатель; 4 — резиновая прокладка; 5— крышка; 6— рычажное устройство; 7— щетка; 8— корпус; 9 — заземляющий болт; 10 —- крышка буксы; 11 — токосъемный диск; 12 — лабиринтное кольцо; 14 — штуцер; 15 — откидной болт
К заземляющему болту 9 подсоединены две щетки и наконечник токоведущего провода. Все токоведущие части изолированы прокладками, а болты, крепящие щеткодержатель, — полихлорвиниловыми трубками, что исключает прохождение силового тока через корпус и буксовые подшипники.
Букса колесной пары прицепного вагона изнутри принципиально такая же, как и букса колесной пары моторного вагона. Основное их отличие состоит в конструкции корпуса буксы. Корпус 2 (рис. 1.46) выполнен тонкостенным и имеет чашки под буксовыми пружинами. Для прохода через них шпинтонов тележки в чашках имеются отверстия, диаметр которых на 20 мм больше, чем диаметр втулок, насаженных на хвостовики шпинтонов. Поэтому достигается свободное, без ударов перемещение буксы относительно рамы и самоустановка буксы за счет поперечной упругости надбуксовых пружин.
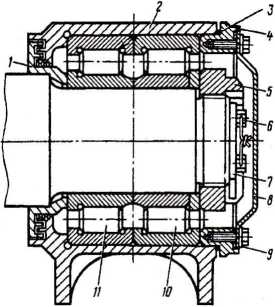
Рис. 1.46. Букса прицепного вагона: 1 — лабиринтное кольцо; 2 — корпус буксы; 3 — уплотнительное кольцо; 4 — крышка; 5— торцовая гайка; 6— проволока; 7— стопорная планка; 8 — смотровая крышка; 9— прокладка; 10, 11 — подшипники
С передней стороны имеются две крышки — смотровая 8 и крепительная — 4. Между корпусом буксы и крышкой 4 устанавливают уплотняющее резиновое кольцо 3. На правой буксе передней колесной пары головного вагона дополнительно смонтирован привод скоростемера ЗСЛ-2М.
Колесные пары. Колесная пара — один из самых ответственных узлов механической части, определяющих безопасность движения электропоезда. Это — опора вагона электропоезда. Шейки оси несут на себе всю нагрузку от веса кузова с пассажирами. Колесные пары жестко воспринимают все удары от неровностей пути (стыки, стрелки и пр.) и в то же время сами жестко воздействуют на путь. Кроме того, колесные пары моторных вагонов преобразуют вращательное движение, передаваемое от тяговых двигателей, в поступательное движение всего электропоезда, а при электрическом торможении воспринимают замедляющее усилие от тяговых двигателей для остановки поезда.
Колесная пара формируется из следующих элементов: ось, два колесных центра, бандажи (или безбандажные цельнокатаные колеса). Кроме того, на оси колесной пары моторного вагона имеется зубчатое колесо и подшипниковый узел опоры редуктора тяговой передачи. В зависимости от конструкции колесного центра колесные пары разделяются на спицевые, дисковые и цельнокатаные.
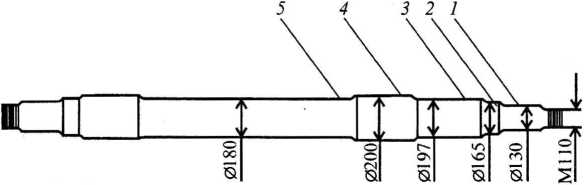
Рис. 1.47. Схематичный рисунок оси колесной пары моторного вагона: 1 — шейка оси; 2— предподступичная часть оси: 3— подступичная часть; 4 — шейка под опорные подшипники редуктора; 5— средняя часть оси
Ось колесной пары имеет несколько участков с различными диаметрами (рис. 1.47): буксовые шейки 1, предподступичные части 2, подступичные части 3 для напрессовки колесных центров, шейку 4 под опорные подшипники редуктора и среднюю часть 5. Переходы от участка одного диаметра к другому выполнены в виде плавных закруглений (галтелей) для уменьшения возникающих напряжений в металле. Оси вагонов работают в тяжелых условиях. Поэтому буксовые шейки, предподступичные части и подступичные части, галтели, а также среднюю часть оси подвергают упрочнению накаткой роликами в заводских условиях на специальных токарных станках, которые имеют измерительные устройства для контроля усилий накатки. При этом поверхностный слой упрочняется на глубину 4…б мм, увеличивается твердость поверхности, что значительно повышает долговечность срока службы оси.
При формировании, ремонте и освидетельствовании колесных пар на оси наносят четкие клейма согласно стандарту и техническим условиям. Клейма также ставят на бандажах, ободах безбандажных колес, венцах зубчатых колес. На необработанных осях клейма наносят на среднюю часть и подступичные части, после обработки клейма и знаки переносят на торец оси с правой стороны.
Правой стороной оси считают ту, на которой имеются клейма, относящиеся к ее изготовлению. Клеймение колесных пар производят работники, имеющие право освидетельствования колесных пар. На рис. 1.48… 1.51 показаны знаки и клейма на наружной грани бандажа, на торце ступицы колесного центра и на боковой поверхности обода цельнокатаного колеса. При формировании, а также освидетельствовании колесной пары с распрессовкой оси и при полном освидетельствовании дополнительные клейма ставят на левом торце оси (клейма приемщиков, номер пункта, дата освидетельствования), они должны сохраняться во время эксплуатации.
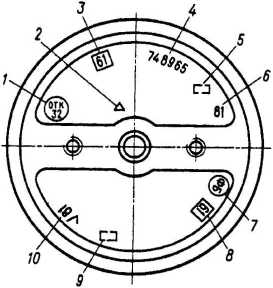
Рис. 1.48. Знаки и клейма на правом торце оси колесной пары: 1 — клейма приемки ОТК; 2 — клейма правильного переноса знаков маркировки; 3— номер завода; 4— порядковый номер оси; 5— клейма приемщика МПС; 6— год изготовления; 7— клейма формирования и балансировки; 8 — номер предприятия, сформировавшего колесную пару; 9 — клейма приемки; 10 — дата формирования
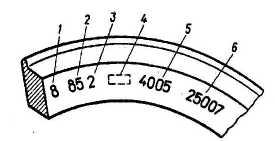
Рис. 1.49. Знаки и клейма на наружной грани бандажа: 1 — номер завода-изготовителя; 2— год изготовления; 3— марка бандажа; 4 — клейма приемки; 5— номер плавки; б— номер бандажа
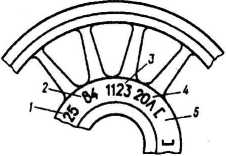
Рис. 1.50. Знаки и клейма на наружном торце ступицы: 1 — номер завода-изготовителя; 2 — год изготовления; 3 — номер колесного центра; 4 — марка стали; 5 — клейма технического контроля
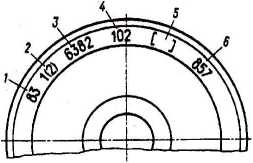
Рис. 1.51. Знаки и клейма на боковой поверхности обода цельнокатаного колеса: 1 — год изготовления; 2 — марка стали; 3 — номер плавки; 4 — номер завода-изготовителя; 5— клейма технического контроля; 6— порядковый номер колеса
Колесо моторного вагона (рис. 1.52) состоит из колесного центра 2, сменного бандажа 4 и бандажного кольца 5. В колесный центр входит ступица для насадки на ось, которая может быть удлиненной (на поездах ЭР2) или нормальной (на поездах ЭР2Т, ЭД2Т, рис. 1.53). Одиннадцать спиц соединяют ступицу колесного центра с ободом, на который насаживают бандаж. К фланцу ступицы призонными болтами прикрепляют зубчатое колесо.
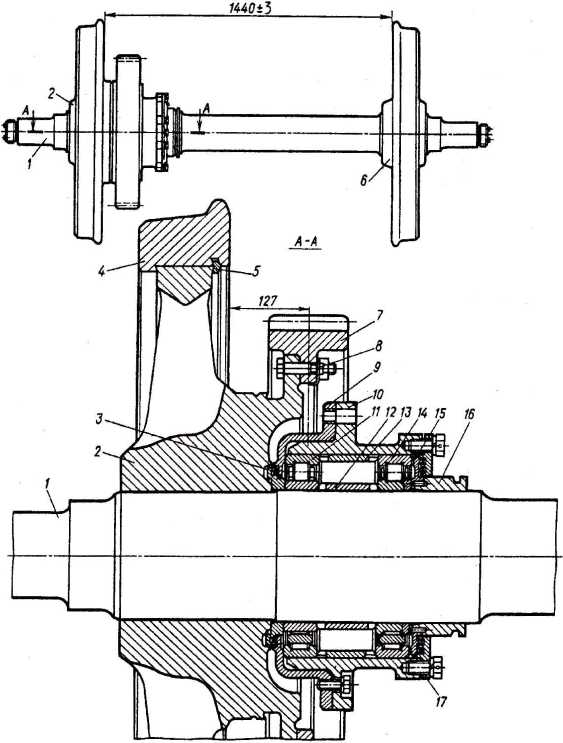
Рис. 1.52. Колесная пара моторного вагона электропоезда ЭР2: 1— ось; 2, 6— колесные центры; 3— лабиринтное кольцо; 4— бандаж; 5— бандажное кольцо; 7 — зубчатое колесо; 8 — призонный болт; 9, 16 — упорные крышки; 10—стакан; 11 — роликовый подшипник; 12—внутреннее распорное кольцо; 13 — наружное разрезное кольцо; 14 — роликовый подшипник; 15 — уплотнительное кольцо; 17— лабиринтная крышка
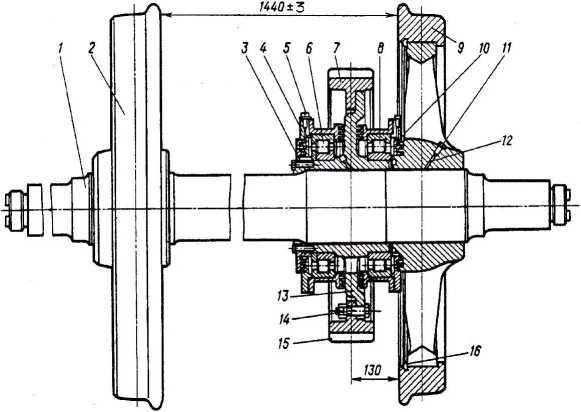
Рис. 1.53. Колесная пара моторного вагона электропоезда ЭР2Т: 1 — ось: 2— колесный центр; 3, 4, 10 — лабиринтные крышки; 5— подшипниковая обойма; 6, 8— опорные подшипники; 7— зубчатое колесо; 9— бандаж; 11 — пробка; 12— отверстие в ступице для распрессовки колесного центра; 13— ступица зубчатого колеса; 14 — призонный болт; 15 — венец зубчатого колеса; 16 — бандажное кольцо
Ширина обода колесного центра — 88 мм, наружный диаметр — 900 мм, внешний диаметр обода должен быть примерно на 1,1… 1,4 мм больше, чем внутренний диаметр бандажа. Диаметр поверхности катания нового бандажа составляет 1050 мм, ширина бандажа — 130 мм. Колесные пары прицепных вагонов формируют из цельнокатаных колес, их диаметр по кругу катания составляет 950 мм. По мере износа колеса обтачивают.
Под формированием колесной пары понимают запрессовку оси в колесные центры, насадку бандажей и окончательную обточку. Материалом бандажей служит высококачественная углеродистая сталь, потому что он должен быть довольно твердым, чтобы выдерживать ударные нагрузки, и в то же время — достаточно вязким. Бандажи прокатывают из стальных заготовок и перед посадкой нагревают до температуры 250…320 °C. Их насаживают на обод колесного центра так, чтобы бурт 3 упирался в обод 2 (рис. 1.54). При температуре не ниже 150…200 °C устанавливают бандажное кольцо 1 фасонного профиля (кольцо нельзя ставить на холодный или остывший бандаж).
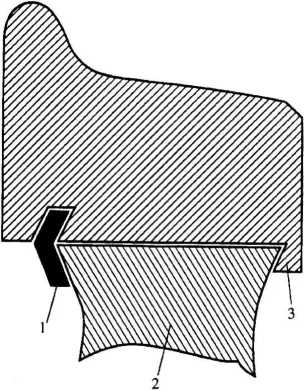
Рис. 1.54. Фиксация бандажа на колесном центре: 1 — фасонное разрезное кольцо; 2— обод колесного центра; 3— бурт бандажа
Концы кольца зачеканивают, они должны точно подходить друг к другу, образуя так называемый замок. Затем бурт выточки бандажа обжимают на вальцовочном станке, чтобы зафиксировать кольцо, после чего следует медленное естественное охлаждение. Бандажное кольцо 1 (рис. 1.54) препятствует поперечному сдвигу бандажа с колесного центра в наружную сторону, а бурт бандажа 3 не позволит ему сдвинуться внутрь колесной пары. После остывания плотность насадки бандажа и кольца проверяют на слух, обстукивая всю поверхность бандажа слесарным молотком.
Для контроля за возможным сдвигом бандажа в эксплуатации на ободе колесного центра напротив одной из спиц наносят контрольную метку затупленным зубилом. На бандаже (на продолжении линии контрольной метки) делают четыре-пять углублений керном. Затем в этом месте бандажа проводят красную полосу шириной 25 мм.
Ослабление или сдвиг бандажа может произойти из-за нарушения технологии насадки, недостаточного натяга, попадания между посадочными поверхностями окалины, песка, грязи. Новые бандажи в эксплуатации, как правило, не доставляют неприятностей, хотя и они могут ослабевать и проворачиваться. Больше беспокоят изношенные бандажи, которые систематически при торможении перегреваются и ослабевают (от перегрева такой бандаж даже меняет свой цвет).
Обладая определенным опытом осмотра механической части, ослабление бандажа можно определить по глухому дребезжащему звуку при обстукивании молотком. Если появились сомнения в исправности, необходимо проверить совпадение контрольных отметок на бандаже и ободе. В эксплуатации, предполагая ослабление бандажа, на ободе и бандаже ставят мелом контрольную риску и при каждой возможности проверяют ее положение.
Запрессовку оси в колесные центры или цельнокатаные колеса проводят в холодном состоянии. Перед этим посадочные поверхности очищают, шлифуют и смазывают олифой или растительным маслом (подсолнечным или льняным). Посадочный диаметр ступицы должен быть на 0,1 …0,3 мм меньше диаметра подступичной части. При запрессовке отверстие ступицы раздается, а ось сжимается на величину натяга. Натяг является определяющим фактором холодной посадки.
Усиление запрессовки зависит также от длины диаметра сопрягаемых частей, для колесных пар моторных вагонов оно составляет 750… 1000 кН, прицепных вагонов — 600…900 кН. Усилия запрессовки обязательно контролируют, для этого на гидравлическом прессе имеется индикаторное устройство для снятия диаграммы, по которой судят о прочности насадки. Удовлетворительная диаграмма представляет собой плавную кривую, свидетельствующую о нарастании усилия по мере продвижения детали. Если на диаграмме имеются площадки, вогнутости или впадины, говорящие о продвижении деталей без усилия, или скачкообразные повышения усилий (больше нормы), ее считают неудовлетворительной, а колесную пару бракуют и распрессовывают.
Перечень прессовых работ при ремонте и формировании колесных пар, а также иллюстрация и объяснение индикаторных диаграмм подробно приведены в Инструкции по формированию, ремонту и содержанию колесных пар № ЦТ 329 от 1995 г.
Так как бандаж соприкасается с рельсом на относительно малой площади, при больших нагрузках происходит естественный износ колеса, который нарушает нормальное качение. Внешняя поверхность бандажа называется поверхностью катания, ее делают конической с конусностями 1:10 и 1:3,5 (рис. 1.55). Это позволяет колесной паре самоустанавливаться в рельсовой колее на прямых участках пути и улучшает прохождение кривых, уменьшая пробуксовку, а следовательно, и износ бандажа. Рабочей поверхностью катания является участок с конусностью 1:10. Наружная часть бандажа с конусностью 1:3,5 изнашивается мало, так как работает только в кривых небольшого радиуса и облегчает нормальное прохождение стрелочных переводов при большом износе (прокате) колеса.
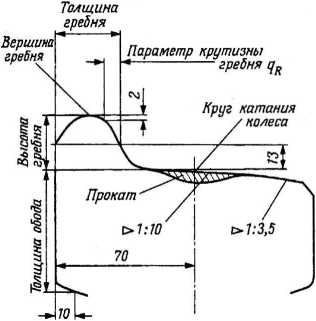
Рис. 1.55. Профиль поверхности катания колеса и контролируемые параметры
Геометрические параметры поверхности катания необходимо строго контролировать. В случае изменения профиля катания колесную пару выкатывают и обтачивают на станке. Вначале обрабатывают внутреннюю торцевую грань, гребень и поверхность катания бандажа или обода цельнокатаного колеса. Затем профиль проверяют с помощью шаблона. Обточку можно произвести и без выкатки колесной пары.
Рассмотрим более подробно геометрию бандажа. Круг катания колеса — это круг, образованный пересечением поверхности катания колеса с вертикальной плоскостью на расстоянии 70 мм от внутренней грани бандажа (точнее — это внешняя окружность сечения, показанного на рис. 1.55 штрих-пунктирной линией).
Высота гребня — это расстояние между вершиной гребня и горизонталью, проходящей через круг катания колеса. На колесных парах электропоездов высота гребня равна 28 мм и очевидно, что с увеличением проката высота гребня будет увеличиваться.
Толщину гребня традиционно измеряли абсолютным шаблоном в сечении гребня на расстоянии 18 мм от его вершины (толщина гребня должна быть в пределах 25…33 мм). В настоящее время используют универсальный шаблон УТ-1, которым толщину измеряют в сечении на заданном расстоянии от поверхности катания колеса. Это — расстояние, измеренное по горизонтали на высоте 13 мм от круга катания колеса между двумя точками, лежащими по разные стороны от вершины гребня. Одна точка находится на плоскости внутренней грани бандажа, другая — на наружной поверхности гребня (см. рис. 1.55). В этом случае толщина гребня должна быть 23.. .31 мм.
При использовании абсолютного шаблона уровень измерения остается на расстоянии 18 мм от вершины гребня. В случае использования шаблона УТ-1 уровень измерения толщины гребня удаляется от вершины гребня по мере увеличения проката. Такой метод оценки геометрических параметров гребней колес является более прогрессивным. (При прокате 3 мм замеры линии толщины гребня обоими шаблонами совпадают.)
Инструкцией по содержанию колесных пар № ЦТ 329 введен важный геометрический параметр qR (крутизны наклона гребня), определяющий безопасное качение колеса, в частности — безопасное прохождение колесом стрелочных переводов в противошерстном движении. Это расстояние, определяемое шаблоном УТ-1, измеряется по горизонтали (не по вертикали!) между двумя точками наружной поверхности гребня, одна из них находится в 2 мм от вершины, другая -в 13 мм от круга катания колеса. Крутизна гребня qR — параметр комплексный. Это означает, что он характеризует не только изменения формы (изменения угла наклонной плоскости) и размеров гребня, но и всего профиля катания колеса, связанного с износом в эксплуатации.
Согласно инструкции расстояние qR не должно быть меньше 6,5 мм. Если, допустим, оно оказалось равным 8 мм, это означает, что все геометрические параметры профиля поверхности катания находятся в норме. Если оно оказалось равным 5 мм, колесо не пригодно к эксплуатации.
Расстояние от горизонтали, проходящей через круг катания до основания посадочной поверхности, является толщиной бандажа (или обода).
Для определения технического состояния и пригодности колесных пар к эксплуатации их неоднократно осматривают:
- под подвижным составом — при всех видах ТО и ТР и при каждой проверке в эксплуатации;- обыкновенное освидетельствование колесных пар — во всех случаях переподкатки под электропоезд;
- полное освидетельствование колесных пар — при ремонтах на заводах, смене одного из элементов, при неясности клейм и знаков, повреждениях после крушений, столкновений, аварий или схода вагона;
- освидетельствование с распрессовкой оси необходимо в случае непрозвучивания оси ультразвуком, при снятии обоих колесных центров, неясности клейм формирования.
Перечислим тех, кто должен осматривать колесные пары:
- машинист — при каждой приемке моторвагонного подвижного состава в доступных местах по доступной осмотру стороне, в эксплуатации — при стоянках на станциях и в пунктах оборота, при ТО-2;
- мастер — при ТО-3;
- мастер и приемщик локомотивов — при ТО-4, ТО-5, ТР-1, ТР-2, при первой подкатке новой колесной пары.
В ходе осмотра бандажей проверяют отсутствие трещин, ползунов, плен, раздавленностей, вмятин, отколов, раковин, выщербин, ослабления бандажей (остукиванием молотком), сдвига бандажа (по контрольным рискам на бандаже и ободе). Контролируют также предельный прокат или износ, вертикальный подрез гребня, ослабление бандажного кольца, опасную форму гребня, остроконечный накат. Опасную форму гребня контролируют шаблоном УТ-1 при всех видах технического обслуживания в депо и текущих ремонтах, а также при ежемесячных обмерах колесных пар.
Об ослаблении бандажа можно судить по следующим признакам:
- появляется глухой дребезжащий звук при остукивании молотком обода колесного центра и бандажа;
- нарушен слой краски или выделяется смазка, ржавчина по окружности прилегания бандажа к ободу;
- образовался зазор между ободом колесного центра и упорным буртом бандажа;
- не совпадают контрольные риски на бандаже и ободе колесного центра.
При ослаблении посадки ступицы на оси возможны:
- выделение смазки или ржавчины вокруг ступицы с внутренней стороны или нарушение краски в месте сопряжения оси со ступицей;
- изменение расстояния между внутренними гранями бандажей, это обнаруживают по прижатию гребней обоих колес к рельсам или по набеганию на гребни тормозных колодок;
- уменьшение расстояния от переходной галтели подступичной части оси до наружного торца ступицы.
При образовании трещины в подступичной части ржавчина обычно выделяется в виде красноватой пыли, нарушается слой краски или она вздувается в месте сопряжения оси со ступицей (подповерхностная коррозия).
Отсутствие трещин проверяется также на колесных центрах, цельнокатаных колесах, в спицах, дисках, ступицах, ободах: нет ли поперечных, косых и продольных трещин, плен, протертых мест, электрических ожогов на открытых частях оси. Убеждаются также в отсутствии нагрева букс, обращают внимание на состояние зубчатой передачи, нет ли нагрева подшипников редуктора (сразу после постановки на смотровую канаву).
В соответствии с ПТЭ расстояние между внутренними гранями колес должно быть (1440 ± 3) мм. Запрещено выпускать подвижной состав после ТО-2, ТО-3 и всех видов ТР и допускать к эксплуатации с трещинами в любой части оси колесной пары, ободе, диске, ступице и бандаже, а также при следующих износах и повреждениях колесных пар:
- прокат более 8 мм;
- толщина гребня, измеренная на расстоянии 18 мм от его вершины, более 33 мм или менее 25 мм;
- ползун на поверхности катания более 1 мм.
При обнаружении на колесной паре прицепного вагона в пути следования ползуна более 1, но менее 2 мм разрешается довести состав до ближайшей станции технического обслуживания со скоростью не более 100 км/ч. Если на прицепном вагоне образовался ползун от 2 до 6 мм, а на моторном от 1 до 2 мм, допускается следование до первой станции со скоростью не более 15 км/ч. При ползунах от 2 до 4 мм на моторном и от 6 до 12 мм на прицепном вагонах следуют до первой станции со скоростью не более 10 км/ч. При ползунах на моторном вагоне более 4 мм, на прицепном — более 12 мм разрешается следование со скоростью не более 10 км/ч при условии, что колесная пара исключена из вращения.
К перечню повреждений колесной пары также относятся:
- выщербина, раковина, вмятина на поверхности катания глубиной более 3 мм или длиной более 10 мм на моторном вагоне и более 25 мм на прицепном вагоне;
- выщербина, вмятина на вершине гребня длиной более 4 мм;
- разница в прокатах правой и левой стороны колесной пары более 2 мм;
- опасная форма гребня;
- остроконечный накат;
- вертикальный подрез гребня, измеряемый специальным шаблоном, более 18 мм от поверхности катания;
- местное или общее уширение бандажа или обода цельнокатаного колеса более 6 мм;
- протертое место на средней части оси более 2,5 мм;
- ослабление бандажного кольца в сумме по длине более 20% и на расстоянии менее 100 мм от замка;
- кольцевые выработки на поверхности катания у основания гребня глубиной более 1 мм, на конусности 1:3,5 — глубиной более 2 мм и шириной более 15 мм.
При наличии кольцевых выработок на других участках поверхности катания нормы браковки — как для кольцевых выработок, расположенных у гребня.
Минимальная толщина бандажей колесной пары моторного вагона должна быть 35 мм, обод цельнокатаного колеса на прицепном вагоне должен быть 25 мм, допустимая разность диаметров бандажей, измеренная по кругу катания:
- на одной колесной паре составляет 0,5 мм (в эксплуатации — до 3 мм);
- у одной тележки моторного вагона — 8 мм; прицепного вагона — 15 мм.
У колесных пар разных тележек моторного вагона допускается разность 15 мм, прицепного вагона — 30 мм.
Обнаруженные дефекты фиксируют в журнале ТУ-152 и книге ремонта ТУ-28. На колесных парах не реже одного раза в месяц замеряют прокат, толщину гребней, параметр крутизны (опасную форму) гребня. Один раз в квартал измеряют диаметры колес. Чтобы уяснить важность перечисленных неисправностей, приводим их краткие характеристики.
Прокат. Это естественный и нормальный износ колеса в эксплуатации за счет деформации и истирания от рельсов и тормозных колодок. Прокат измеряется абсолютным шаблоном на расстоянии 70 мм от внутренней грани бандажа (т.е. по кругу катания), так как в этой зоне прокат наибольший. Этим же шаблоном можно определить прокат у самого гребня и у наружной грани бандажа. Поэтому им удобно пользоваться при измерении ползуна. Прокат ухудшает плавность хода, особенно на кривых участках пути. Появляется опасность схода при проследовании стрелочных переводов, увеличивается боксование колесных пар моторных вагонов, т.е. их износ.
Прокат измеряют также шаблоном УТ-1. Но поскольку его опора жестко закреплена на расстоянии 70 мм от внутренней грани бандажа, прокат фиксируют только по кругу катания. Для этого данным шаблоном определяют фактическую высоту гребня и из нее вычитают чертежный размер высоты. Полученная разность укажет величину проката П. Например, если измеренная высота гребня h = 32 мм, а чертежный размер высоты нового гребня колесной пары равен 28 мм, то прокат бандажа
П = h— 28 = 4 мм.
Ползуны (выбоины). Они образуются на поверхности катания при заклинивании колесной пары, которое возможно из-за неправильного управления тормозами, при движении на грязных рельсах, заклинивании зубчатой передачи, разрушении якорных подшипников двигателя, неисправностях тормозных приборов или авторегулятора (т.е. рычажной передачи) и т.д. Глубина ползуна определяется сравнением замеров абсолютным шаблоном в месте ползуна и по этой же окружности в другом месте, где его нет.
Опасная форма гребня (параметр крутизны). Поскольку гребни удерживают колесную пару в рельсовой колее, к геометрической форме гребня предъявляются самые высокие требования. Универсальный шаблон УТ-1 позволяет измерить параметр крутизны гребня, по этому параметру судят и о других износах рабочей поверхности бандажа. Если данный параметр окажется менее 6,5 мм, колесную пару бракуют.
Вертикальный подрез гребня. Если на участке обращения много кривых, то наблюдается интенсивный ненормальный износ гребня, в его нижней части появляется так называемый вертикальный подрез. При этом вместо наклонной поверхности гребня образуется вертикальная площадка. В кривых участках пути колесо по наклонной плоскости может несколько вползти на рельс, но возникает жесткий удар, и колесная пара сойдет с рельсов. Бандаж с подрезанным гребнем (как и с остроконечным накатом) представляет большую угрозу для противошерстных стрелочных переводов: он ударяет по остряку, выкрашивает конец остряка, набегает на него, отжимает от рамного рельса и вызывает сход. Высота, толщина и геометрия гребня рассчитаны так, чтобы колесная пара надежно удерживалась в кривых, на стрелочных переводах и т.д.
Если бандаж (или колесо) имеет вертикальный подрез, то параметр крутизны гребня qR будет меньше нормы. Кроме шаблона УТ-1 инструкцией по содержанию колесных пар введен шаблон ДО-1 допускового контроля крутизны гребня взамен ранее применявшегося специального шаблона для выявления вертикального подреза гребня. Шаблон ДО-1 не дает численного значения параметра крутизны, а только оценивает его предельную величину с точки зрения безопасности движения, т.е. шаблон устанавливает, какую форму (опасную или безопасную) имеет гребень.
Изношенный бандаж (колесо) не бракуется, если выступ шаблона высотой 2 мм и длиной 6,5 мм не соприкасается с верхней частью гребня (между ними имеется зазор (рис. 1.56, а). Для установки шаблона в рабочее положение его размещают на гребне бандажа так, чтобы шаблон частью окружности радиусом 15 мм заходил на выкружку гребня, и повертывают до контакта с вершиной гребня. Бандаж (колесо) бракуется, если указанный выступ шаблона касается вершины гребня (рис. 1.56, б).

Рис. 1.56. Контроль параметра крутизны гребня шаблоном ДО-1: а — нормальный гребень; б— бракованный гребень
Остроконечный накат. Это такой вид повреждения, когда у вершины гребня с наружной стороны образуется второй маленький гребешок — ненормальный износ колеса. Раньше его определяли на ощупь. Теперь остроконечный накат можно обнаружить шаблоном УТ-1. Выкатка колесной пары в данном случае обязательна.
Толщина гребня. При естественном износе толщина особенно интенсивно уменьшается при разнице диаметров левого и правого колес, а также при большой работе электропоезда в кривых. Восстанавливают данный параметр обточкой и наплавкой.
Кольцевая выработка. Она образуется на поверхности катания в условиях повышенной влажности при посторонних включениях в тормозных колодках. Замеряют выработки толщиномером и линейкой, устраняют — обточкой с выкаткой колесной пары.
Навар (натаск). Это — смещение металла на поверхности катания при кратковременном юзе. Он сопровождается большим нагревом и закалкой поверхности из-за быстрого охлаждения. Высота навара допускается до 0,5 мм.
Выщербина. Выкрашивание участков металла на поверхности катания возникает в результате отслоения тонкого поверхностного слоя металла.
Раковина. Она образуется на поверхности катания из-за недоброкачественной отливки или плохой прокатки бандажа или обода цельнокатаного колеса на заводе. Раковина проявляется после износа или обточки верхнего слоя поверхности катания.
Трещина. Опасна тем, что всегда развивается и наступает излом.
На рис. 1.57 показаны некоторые замеры колесных пар: измерения толщины бандажа (а), ширины бандажа (б) и расстояния между внутренними гранями бандажей (в).
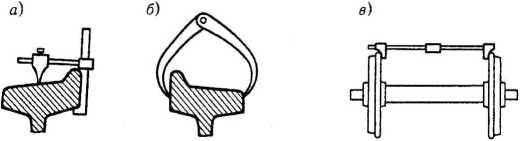
Рис. 1.57. Измерение толщины (а), ширины бандажа (б) и расстояния между внутренними гранями колес (в)
Подвешивание тяговых двигателей и тяговая передача. На электросекциях ранних выпусков тяговый двигатель (ТД) одной стороной прикрепляли к поперечной балке тележки, а другой он опирался через подшипники скольжения на ось колесной пары. Такая подвеска называлась опорно-осевой (или “трамвайной”) и отрицательно сказывалась на работе двигателей. Поскольку ТД жестко воспринимал все удары колесной пары, неудовлетворительно работал щеточно-коллекторный аппарат и, например, при прохождении стрелочных переводов требовалось выключать двигатели.
При опорно-осевой подвеске малая цистерна насаживалась непосредственно на выступающий вал двигателя, и во время движения вагона расстояние между осями малой шестерни и большого зубчатого колеса не менялось, так как ТД и колесная пара совершали одни и те же колебания. Поэтому в тяговой передаче отсутствовало дополнительное звено — упругая муфта. Кожух редуктора выполнялся тонкостенным, поскольку он не нес больших нагрузок, а, главным образом, сохранял смазку для зубчатых колес.
В настоящее время применяется так называемая опорно-рамная подвеска ТД, когда он жестко закреплен на поперечной балке тележки и его масса оказывается полностью подрессоренной за счет буксового рессорного подвешивания. Применение такой подвески значительно снижает удары, передаваемые на двигатель, но ТД и колесная пара совершают различные колебания при движении вагона. Поэтому потребовалась мощная несущая конструкция корпуса редуктора, гарантирующая постоянство межцентрового расстояния в зубчатой передаче.
Важным недостатком такой подвески является необходимость упругого звена в тяговой передаче, которое компенсировало бы разницу в перемещениях валов двигателя и малой шестерни при движении. В качестве упругого звена служит резинокордная муфта, которая, кроме того, является соединительным звеном между двигателем и редуктором. За счет упругости она снижает динамические нагрузки в приводе при трогании поезда и при электрическом торможении.
Тяговый двигатель 6 (рис. 1.58) в верхней части остова имеет две опорные лапы 4, которые притягиваются к приваренным выступам поперечной балки тележки двумя клиньями 5. Клинья распирают болты Я головки которых упираются в упор 8, приваренный на поперечной балке. Клинья должны быть плотно прижаты болтами, а болты— законтрены во избежание поворачивания.
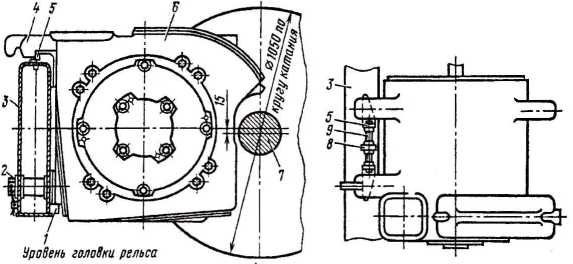
Рис. 1.58. Подвеска тягового двигателя: 1 — кронштейн; 2— болт; 3— поперечная балка рамы тележки; 4 — опорная лапа тягового двигателя; 5— клин; 6— тяговый двигатель; 7— ось колесной пары; 8— упор; 9— болт
В нижней части двигателя на одной линии с лапами имеются две опорные площадки с просверленными в них отверстиями с резьбой М36 под болты 2. Опорными поверхностями остов двигателя опирается на поддерживающие кронштейны поперечной балки рамы и болтами 2плотно притягивается к балке. Такое крепление двигателя (снизу болтами, сверху клиньями) обеспечивает надежное крепление остова к тележке.
Тяговая передача состоит из редуктора 8 и упругой муфты 3 (рис. 1.59). Большое зубчатое колесо 7 насажено на ось колесной пары 6 и находится в зацеплении с малой шестерней 5. Вал малой шестерни закреплен в подшипниках, установленных в корпусе редуктора 8. Редуктор одной стороной опирается на подшипники, расположенные на колесной паре, другой подвешивается к раме тележки на амортизаторах 4. Вал тягового двигателя 1 соединен с валом малой шестерни упругой муфтой 3.
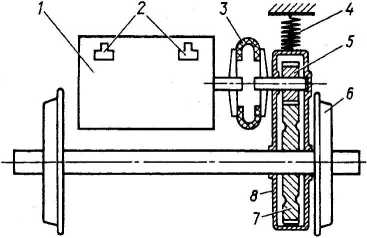
Рис. 1.59. Схема тяговой передачи: 1 — тяговый двигатель; 2— лапы двигателя; 3— упругая муфта; 4— условное изображение шарнирной подвески редуктора; 5— малая шестерня: 6 — колесная пара; 7— большое зубчатое колесо; 8— корпус редуктора
Вращающий момент передается зубчатой передачей (малая шестерня имеет 22 зуба, большое колесо — 75 зубьев). Передаточное число зубчатой передачи (3,41) показывает, во сколько раз уменьшается число оборотов при передаче вращения от двигателя к колесной паре. Зубчатое колесо представляет собой венец, прикрепленный к фланцу ступицы 15колесного центра одиннадцатью призонными болтами. Эти болты имеют небольшую конусность и входят в отверстия с натягом. Гайки болтов застопорены от самоотвинчивания разрезными шайбами.
Венцы зубчатых колес изготавливают из хромоникелевой стали 30ОХНЗА. Заготовки венцов подвергают термообработке с последующим отпуском, затем нарезают зубья и шлифуют их рабочие поверхности на специальном зубошлифовальном станке. Для увеличения срока службы венца производят закалку зубьев на глубину 4…5 мм. После обработки зубья проверяют на отсутствие трещин магнитной дефектоскопией.
Поскольку наиболее ответственные и дорогостоящие детали в любом редукторе — зубчатые венцы, повышению их надежности уделяют много внимания — увеличению степени точности зубчатого зацепления и качества изготовления венца, в первую очередь эвольвентных поверхностей зубьев. Внедряется современный метод ионной цементации, который обеспечивает требуемую твердость и отсутствие закалочных трещин. Геометрию зубчатых колес контролируют электронными зубоизмерительными устройствами.
Малая шестерня состоит из венца и вала с коническим хвостовиком (конусность 1:10). Венец выполнен из стали 12ХНЗА, вал — из стали Ст-45 с последующей термообработкой. После нагрузки зубьев на фрезерном станке зубья шестерни цементируют на глубину 1,5…2 мм и закаляют. После термообработки зубья, впадины и конусные поверхности шлифуют, посадочные поверхности малой шестерни (конус для посадки вала, шейки под роликовые подшипники, хвостовик для посадки фланца муфты) также шлифуют. Перед посадкой венца шлифовальные конусные поверхности притирают. Обработанный венец нагревают в масле до 110… 120 °C и напрессовывают на вал. После посадки в горячем состоянии зубчатый венец должен сесть на 1,2… 1,7 мм глубже, чем при пробной холодной посадке.
Оба зубчатых колеса заключены в стальной литой (или сварной) корпус. Так как корпус является несущей конструкцией, его боковые стенки имеют толщину 12 мм с усиливающими ребрами жесткости, которые подходят к горловине. Корпус состоит из двух половин, соединенных между собой болтами, и они как одно целое охватывают ось колесной пары вместе с большим зубчатым колесом. Верхняя часть корпуса со стороны малой шестерни шарнирно соединяется с поперечной балкой рамы тележки. Удлиненная часть верхней половины (хвостовик) связана со стержнем подвески, а затем — с балкой тележки (рис. 1.60).

Рис. 1.60. Узел подвески редуктора электропоезда ЭР2Т: 1 — амортизатор; 2— пружинная шайба; 3, 9, 15— болты; 4, 13 — гайки; 5— стопорная шайба; 6— стержень; 7— полукольцо; 8, 10 — кольца; 11 — предохранительная скоба; 12— шайба; 14— шплинт; 16 — пластина; 17— кронштейн, приваренный к поперечной балке тележки; 18— корпус редуктора
Такая подвеска редуктора допускает необходимый поворот корпуса относительно оси колесной пары в зависимости от прогиба пружин рессорного подвешивания. Поэтому все перемещения вала двигателя по отношению к валу малой шестерни при движении вагона воспринимает упругая муфта, и работа зубчатой передачи не нарушается.
Стержень подвески соединяет верхний и нижний узлы подвешивания редуктора (стержень иногда называют главным болтом редуктора). Верхний узел, которым подвесной стержень присоединяется к кронштейну балки тележки, состоит из двух резинометаллических амортизаторов 1, двух специальных гаек 4, двух стопорных шайб 5 с шестиугольным отверстием, двух болтов 3, двух пружинных шайб 2. Амортизаторы зафиксированы штифтами, запрессованными в кронштейн рамы. Стержень имеет запас резьбы, что позволяет приподнимать или опускать хвостовик редуктора, иными словами, регулировать наклон упругой муфты.
Нижний узел подвесного стержня включает в себя два резинометаллических амортизатора, четыре полукольца 7, два кольца 10, скобу и крепежные детали, которые фиксируют стержень 6, проходящий через отверстие в хвостовике редуктора. Чтобы предохранить редуктор от падения на путь в случае обрыва стержня или поломки кронштейна, имеется предохранительная пластина (скоба) 11. Противоположной стороной редуктор опирается на ось колесной пары.
На моторных вагонах ЭР2Т и вагонах серии ЭД опорные подшипники расположены на колесной паре симметрично относительно продольной оси редуктора (рис. 1.61), т.е. слева и справа от зубчатого колеса. Поэтому исключается их перегрузка и дополнительная деформация корпуса редуктора, что благоприятно сказывается на его работе. Надо отметить, что подшипник труднодоступен для осмотра и ремонта, это является недостатком.
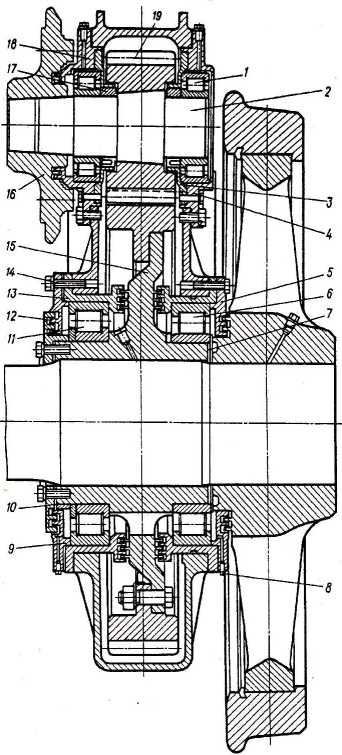
Рис. 1.61. Редуктор электропоезда ЭР2Т: 1, 6, 11 —подшипники; 2 — вал шестерни; 3. 4, 5, 9, 10, 12, 18— крышки; 7 — медная шайба; 8—пробка; 12—лабиринт; 13—обоймы; 14—болт крепления; 15— ступица зубчатого колеса; 16— фланец муфты; 17— дистанционное кольцо; 19 — зубчатый венец шестерни
Вал малой шестерни 2 вращается в двух роликовых подшипниках 1, установленных в корпусе. Подшипники монтируют в крепительных крышках 18, для них в верхней половине корпуса имеются два цилиндрических отверстия. У передней крышки есть отверстие для вала малой шестерни, задняя крышка — глухая. Для удобства сборки и разборки внутренние кольца подшипников установлены на вал с тугой посадкой, наружные — со скользящей. Подшипниковые узлы заполнены смазкой ЖРО. Для ее периодического добавления в крышках имеются штуцеры с пробками.
В боковых стенках корпуса редуктора имеются отверстия, расположенные по окружности. Через них проходят болты 14, которые крепят корпус к обоймам 13 опорных подшипников. В верхней половине редуктора имеется люк для осмотра зубчатой передачи. К крышке люка приварена труба-сапун для выравнивания давления внутри редуктора с атмосферным. В нижней половине корпуса имеется отверстие, через которое добавляют смазку и контролируют уровень заливки. Отработанную смазку сливают через отверстие в боковой стенке корпуса, оба отверстия закрыты резьбовыми пробками. Для смазки роликовых подшипников также предусмотрены отверстия с пробками.
На электропоездах ЭР2 в конструкции редуктора не предусмотрено симметричное расположение опорных подшипников: они располагаются на оси колесной пары по одну сторону от зубчатого колеса (рис. 1.62). С противоположной стороны (со стороны колеса) корпус редуктора опоры не имеет. На колесном центре и корпусе редуктора выполнены лабиринтные уплотнения, препятствующие вытеканию смазки.
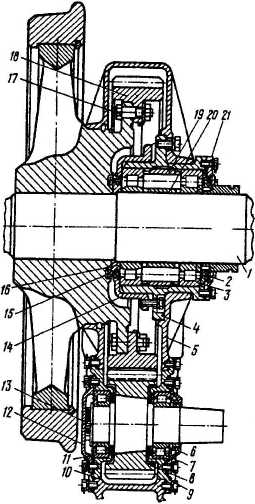
Рис. 1.62. Редуктор электропоезда ЭР2: 1 — ось колесной пары; 2 — лабиринтная крышка; 3 — передний подшипник; 4— стакан; 5— корпус редуктора; 6, 12— передняя и задняя малые крышки; 7— передний подшипник; 8— шестерня; 9— большая крышка; 10— стакан заднего подшипника; 11 — задний подшипник шестерни; 13— шайба; 14— крышка; 15, 21 — лабиринтные кольца; 16 — задний подшипник; 17 — призонный болт; 18 — большое зубчатое кольцо; 19, 20 — наружное и внутреннее распорные кольца
Наличие упругой муфты при опорно-рамной подвеске ТД обязательно, так как резиновая оболочка муфты компенсирует возможную несоосность валов двигателя и малой шестерни при движении вагона. Муфта допускает параллельное смещение валов до 15 мм, продольное — до 20 мм, угловое — до 4 °. Упругая муфта состоит из фланцев 1 и 6(рис. 1.63), резинокордной оболочки 5 и деталей крепления оболочки к фланцам. Оболочка изготовлена из резины с прослойкой кордовой ткани. Ее края усилены стальной армировочной проволокой, фланцы 1 и 6 насажены на конические хвостовики валов двигателя и малой шестерни в горячем состоянии (их нагревают до 140 °C).
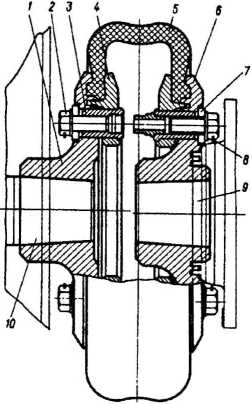
Рис. 1.63. Упругая муфта: 1, 6 — фланцы; 2— болт; 3— втулка; 4— полукольцо (или кольцо); 5 — резинокордный элемент; 7 — шайба; 8 — проволока; 9 — вал шестерни; 10 — вал двигателя
Резиновую оболочку прикрепляют к фланцам со стороны двигателя двумя полукольцами 4, со стороны редуктора — цельным кольцом. Вся конструкция с каждой стороны соединяется восемью болтами 2, вворачиваемыми в запрессованные втулки 3 колец и полуколец. Эти элементы в то же время разгружают болты 2от поперечных срезающих усилий. Для удобства сборки и разборки полуколец и фланцев на болты надеты шайбы 7с прорезью, входящие в углубления фланцев.
Чтобы в эксплуатации муфта надежно работала, важно ее правильно отрегулировать. Поясним, в чем заключается регулировка муфты. За счет упругости резиновой оболочки валы двигателя и редуктора можно несколько приблизить друг к другу и сделать муфту более узкой, но немного увеличенной в диаметре. Возможно, напротив, отдалить валы друг от друга, тогда муфта станет шире по фланцам. Этого добиваются смещением тягового двигателя вдоль его оси. Поскольку отверстия под болты, крепящие ТД к поперечной балке рамы тележки, овальные, двигатель можно перемещать в определенных пределах. Правила ремонта строго устанавливают ширину муфты по фланцам — 171… 177 мм.
При сборке тележки и монтаже двигателя и редуктора с колесной парой необходимо также обеспечить предварительный наклон муфты, т.е. опустить вал малой шестерни по отношению к валу ТД на 2.. .4 мм (верхняя часть муфты должна быть наклонена в сторону редуктора). В правилах ремонта так и сказано: “смещение фланцев упругой муфты в вертикальной плоскости под тарой вагона — не менее 2 мм и не более 4 мм”. Если этого не сделать, в эксплуатации муфта долго не проработает: может быть сорван фланец, порвана резиновая оболочка, возможен излом вала малой шестерни и т.д.
Подобное можно объяснить следующим. После посадки кузова рессорное подвешивание сжимается, и тележка садится ниже. Казалось бы, одинаково опустятся вал ТД и конец редуктора с малой шестерней, так как они крепятся к одной и той же поперечной балке тележки. Но если траектория, по которой опускается двигатель, — прямая линия, то малая шестерня, перекатываясь по большому зубчатому колесу, движется по окружности. Путь по окружности больше, чем путь по прямой, поэтому вал шестерни опустится меньше, чем вал двигателя. Следовательно, под нагрузкой (при заполнении вагона пассажирами) муфта выравнивается и занимает нормальное, вертикальное положение.
Перечислим основные, наиболее часто встречающиеся неисправности тяговой передачи: трещина или излом зубьев малой шестерни или большого зубчатого колеса, неисправность (перекос) подшипников с возможным заклиниванием колесной пары, недостаток смазки, излом хвостовиков валов малой шестерни или двигателя, увеличенный осевой разбег подшипников более 1,2 мм, ослабление или потеря болтов, расхождение верхней и нижней половин редуктора, трещина в корпусе, распрессовка фланцев муфты, повреждение упругой оболочки, обрыв и потеря кордовых болтов и др.
Автосцепка и поглощающий аппарат. Вагоны электропоездов оборудованы нежесткой автосцепкой СА-3 (советская автосцепка, третий вариант). Автосцепку СА-3 стали устанавливать на моторвагонных секциях еще в довоенное время, и за многие годы эксплуатации она прекрасно себя зарекомендовала. Если размеры и износы автосцепки контролируют надлежащим образом, неприятностей быть не может.
Автосцепка автоматически соединяет вагоны между собой и передает тяговые или тормозные усилия. Она допускает взаимное вертикальное перемещение в пути следования и сцепление вагонов при разнице в высоте автосцепок до 100 мм. К автосцепному оборудованию относятся также тяговый хомут, поглощающий аппарат, упорные угольники, упорная плита, розетка с центрирующим механизмом и другие детали. Маятниковое устройство центрирующего механизма, выполненное из балочки и двух подвесок, возвращает автосцепку в центральное положение при ее отклонениях и облегчает сцепление вагонов.
Автосцепка представляет собой стальной литой корпус, который состоит из головы, где размещен механизм сцепления, и пустотелого прямоугольного хвостовика с отверстием для клина. Клин соединяет автосцепку с тяговым хомутом поглощающего аппарата. Голова имеет большой 16 и малый 17 зубья (рис. 1.64). Пространство между большим и малым зубьями образует зев автосцепки (контур зацепления). В механизм сцепления входят замок, замкодержатель, собачка (предохранитель от саморасцепа), подъемник замка, валик подъемника, соединяющий болт.
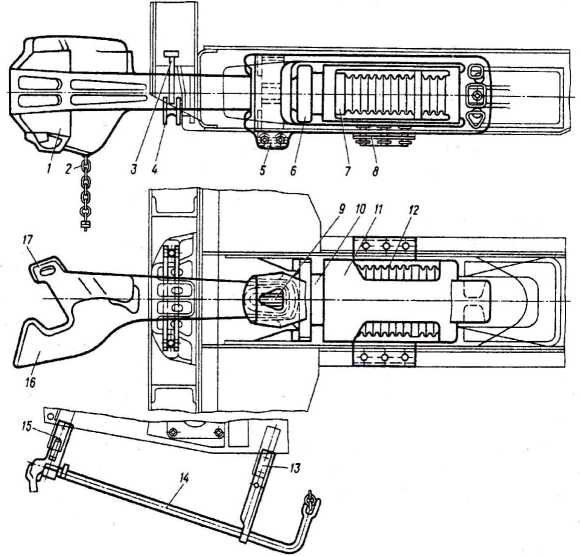
Рис. 1.64. Автосцепка СА-3 и поглощающий аппарат Р-2П: 1 — корпус; 2 — цепь расцепного рычага; 3 — маятниковое устройство; 4 — балка; 5 — тяговый хомут; 6 — упорная плита; 7 — корпус поглощающего аппарата; 8 — поддерживающая планка; 9 — клин; 10 — нажимная плита поглощающего аппарата; 11 — поглощающий аппарат; 12 — резинометаллические элементы; 13, 15 — кронштейны; 14 — расцепной рычаг; 16 — большой зуб; 17 — малый зуб
Назначение деталей автосцепки. Замок — запирает малый зуб соседней автосцепки в пазу большого зуба. Замок установлен в голове автосцепки так, что под действием своей массы стремится опуститься вниз и занять замкнутое положение. Замок имеет сигнальный отросток, окрашенный в красный цвет, на цилиндрический прилив замка навешен предохранитель от саморасцепа (собачка).
Замкодержатель — предотвращает саморасцеп и удерживает автосцепки в расцепленном положении до разведения вагонов. Он имеет овальное отверстие, при помощи которого его навешивают на шип со стороны большого зуба. На замкодержателе имеется лапа, которая видна в зеве автосцепки, и противовес внутри корпуса.
Собачка (предохранитель)— предотвращает саморасцеп в пути следования, имеет прямое и фигурное плечи.
Подъемник замка — служит для расцепления автосцепок, отводит замок внутрь и при помощи замкодержателя не дает ему опуститься и восстановить сцепление вагонов раньше, чем они будут разведены. Подъемник имеет прямой и фигурный пальцы, квадратное отверстие для валика.
Валик подъемника — соединяет все части механизма для расцепления автосцепок.
Болт — удерживает валик подъемника от выпадания. .
Сборка автосцепки. Внутрь головы автосцепки вводят подъемник фигурным пальцем вверх и кладут на опору со стороны большого зуба. Затем вставляют замкодержатель и овальным отверстием навешивают его на шип большого зуба. На шип замка навешивают также собачку, и замок с собачкой устанавливают на опору.
При установке замка необходимо тонким стержнем нажать на фигурное плечо собачки, чтобы ее верхнее прямое плечо оказалось выше противовеса замкодержателя. После размещения замка через отверстие в голове автосцепки со стороны малого зуба пропускают валик подъемника и запирают его болтом. Болт заполняет выемку валика и не позволяет вынуть валик из автосцепки.
Сцепление. Перед сцеплением замок и лапа автосцепки выходят в зев. Верхнее плечо собачки лежит на полочке малого зуба и располагается выше противовеса замкодержателя. При сцеплении вагонов малый зуб одной автосцепки скользит по скошенной поверхности большого или малого зуба другой и входит в зев. Далее он нажимает на замок и вводит его внутрь корпуса, затем нажимает на лапу замкодержателя и освобождает замок.
Замки двух автосцепок под действием своей массы опускаются, выходят из корпуса и расклинивают друг друга, т.е. заполняют свободное пространство в контуре зацепления автосцепок, чем препятствуют обратному выскальзыванию малых зубьев. Так как на лапы замкодержателей нажимают малые зубья, их противовесы в корпусах подняты и расположены против верхних плеч собачек. Это исключает возможность саморасцепа, поскольку в случае толчка замка внутрь корпуса он удержится от перемещения за счет упора собачки в противовес замкодержателя. При этом сигнальные отростки не должны быть видны.
Расцепление. Для расцепления автосцепок необходимо один из замков утопить внутрь головы корпуса, повернув расцепной рычаг. При этом вращаются валик и подъемник, который своим фигурным пальцем нажимает на нижнее плечо собачки. Собачка поворачивается, и ее верхнее плечо становится выше противовеса замкодержателя. Затем подъемник тем же пальцем уводит замок в полость автосцепки, одновременно его прямой палец поднимает замкодержатель. После этого палец заскакивает за угол замкодержателя, который под действием своей массы опускается вниз.
Автосцепки останутся расцепленными, пока не разведут вагоны. Замок будет удерживаться внутри за счет нажатия фигурного пальца подъемника, который обопрется об угол замкодержателя. Снаружи при этом виден сигнальный отросток.
После разведения вагонов малые зубья автосцепок перестают нажимать на лапы замкодержателей. Они освобождаются и поворачиваются, лапы замкодержателя снова выходят в зевы автосцепок, а отошедшие углы освобождают подъемники. Подъемники опустятся, и замки выйдут из корпусов в зевы автосцепок. Теперь автосцепки готовы к повторному сцеплению.
Проверка автосцепки. Установлены два вида осмотра автосцепок: полный — предусматривающий снятие с вагона (при ТР-2, ТР-3 и капитальных ремонтах), когда узлы автосцепки направляют на контрольный пункт для проверки и ремонта, и наружный — без снятия автосцепки. Наружный осмотр проводится при ТО-З.ТР-1, при этом степень износа деталей определяют комбинированным шаблоном.
При наружном осмотре проверяют:
- работу механизма сцепления автосцепки;
- износ тяговой и ударной поверхностей большого и малого зубьев, ширину зева, толщину замка;
- отсутствие трещин и изгибов в корпусе и тяговом хомуте;
- крепление клина тягового хомута;
- прилегание поглощающего аппарата к задним упорам;
- зазор между хвостовиком и потолком ударной розетки (должен быть не менее 25 мм);
- зазор между хвостовиком и окном в концевой балке (должен быть менее 20 мм);
- высоту продольной оси автосцепки и положение оси.
Автосцепку считают неисправной, если она не удовлетворяет требованиям шаблона 940Р, детали имеют трещины. Высота автосцепки должна быть в норме, разница в высотах у одного вагона не должна превышать 25 мм. Провисание автосцепки не должно быть более 3 мм, подъем — не более 5 мм. Эти величины измеряют по оси автосцепки в двух точках: на выходе из розетки и у головы автосцепки. Зазор между замком и вертикальной кромкой малого зуба не должен быть более 8 мм, а зазор между лапой замкодержа-теля и кромкой замка не должен быть менее 16 мм. Маятниковые подвески устанавливают широкими головками вниз, клин должен иметь типовое крепление.
На рис. 1.65 показаны некоторые замеры автосцепки шаблоном. Так, на рис. 1.65, а видно, как контролируют предохранитель замка (действие “собачки”) от саморасцепа: если расположить шаблон, как показано, чтобы он надавливал на лапу замкодержателя, и рукой нажать на замок, пытаясь его втолкнуть в корпус автосцепки, он не должен полностью убраться. В этом случае нормальный ход замка от приложенного усилия должен быть 7… 18 мм, тогда предохранитель считается годным. Если замок полностью входит в корпус — предохранитель неисправен.
На рис. 1.65, б показана проверка толщины замка. Если шаблон одновременно прилегает к боковым сторонам малого зуба и замка, замок негоден (тонкий). На рис. 1.65, я поясняется проверка ширины зева автосцепки. Если шаблон проходит мимо носка большого зуба в зев, то корпус автосцепки негоден. Замеры производят по всей высоте носка большого зуба. На рис. 1.65, г показана проверка износа малого зуба: между шаблоном и малым зубом должен быть зазор, если шаблон прилегает плотно, автосцепка негодна. Точно так же проверяют износ тяговой поверхности большого зуба и ударной поверхности зева автосцепки: если шаблон входит в зев, автосцепку бракуют (эти проверки проводят на расстоянии 80 мм вверх и вниз от продольной оси).
Проверяют также удержание замка в расцепленном положении (работу автосцепки “на буфер”). В этом случае следует приложить шаблон (см. рис. 1.65, а), повернуть подъемник до отказа и освободить рычаг—замок не должен опуститься в зев. Контролируют преждевременное включение предохранителя при сцеплении. Откидной скобой шаблона (35 мм) нажимают на лапу замкодержателя. При этом замок должен уходить в корпус автосцепки.
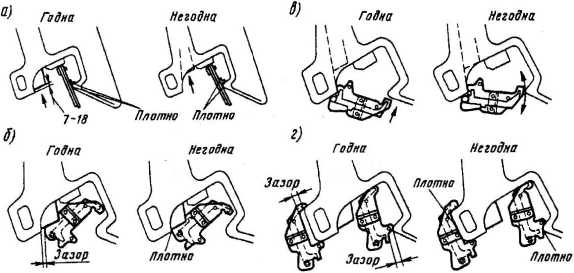
Рис. 1.65. Проверка автосцепки шаблоном: а — проверка исправности предохранителя замка; б — проверка толщины замка; в — проверка ширины зева; г — проверка износа малого зуба и расстояния между тяговой поверхностью большого зуба и ударной поверхностью зева автосцепки
В эксплуатации важно постоянно следить за правильным расположением автосцепки над уровнем головок рельсов. Соблюдение разницы в высоте их осей, установленной ПТЭ, исключает саморасцепы, обеспечивает безопасность движения. Высоту расположения продольной оси автосцепки измеряют специальным шаблоном с линейкой. За продольную ось принимают литейный шов, расположенный на корпусе. Высота оси автосцепок головных вагонов с внешней стороны составляет 990 …1070 мм, промежуточных вагонов— 1080…1160 мм.
Перечислим основные причины, приводящие к саморасцепу:
- расхождение центров автосцепок более нормы;
- сработался торец прямого плеча собачки, упор противовеса или лапа замкодержателя;
- отломился противовес замкодержателя;
- увеличилась ширина зева головы автосцепки;
- уменьшилась из-за износа толщина замка;
- короткая или слишком длинная цепь.
Поглощающий аппарат. Для смягчения ударов и рывков, которые передаются от автосцепок на рамы кузовов вагонов, служат поглощающие аппараты Р-2П или Р-5П. Поглощающий аппарат Р-2П (рис. 1.66) состоит из корпуса 1, нажимной плиты 2, девяти резинометаллических элементов 3 и промежуточной плиты 4. Резинометаллический элемент собран из двух стальных листов толщиной 2 мм, между которыми расположена специальная морозостойкая резина, жестко связанная с листами (резина вулканизированная). Сечение резины по наружному контуру в форме параболы, поэтому предотвращается выход сжатой резины за пределы металлических мостов.
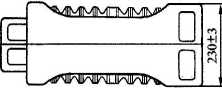
Рис. 1.66. Поглощающий аппарат Р-2П: 1 — корпус; 2 — нажимная плита; 3 — резинометаллические элементы; 4 — промежуточная плита; 5 — днище корпуса
Чтобы при сжатии аппарата исключить относительное смещение резинометаллических элементов и их соприкосновение с кромкой корпуса, на днище корпуса, нажимной и промежуточной плитах, а также на стальных листах резинометаллических элементов имеются фиксирующие выступы и соответствующие углубления.
Собирая аппарат, сначала в корпус 1 сбоку заводят нажимную плиту 2 и устанавливают ее так, чтобы упорная часть полностью выходила из окна корпуса. Затем размещают промежуточную плиту 4 таким образом, чтобы ее заплечики охватывали продольные стенки корпуса. После этого четыре резинометаллических элемента 3 помещают между промежуточной плитой и днищем корпуса. Фиксирующие выступы на элементах должны совпадать с соответствующими углублениями.
Специальной струбциной элементы в корпусе аппарата сжимают через промежуточную плиту 4, чтобы между нажимной и промежуточной плитами 2 и 4 поставить остальные пять резинометаллических элементов. Затем сжатые элементы освобождают от нагрузки, они расправляются и запирают в корпусе пять введенных элементов.
Разбирают аппараты в обратном порядке. Предварительно сжимают через промежуточную плиту четыре резинометаллических элемента, вынимают элементы, которые находятся между нажимной и промежуточной плитами. После снятия нагрузки с промежуточной плиты остальные элементы аппарата легко вынимают из корпуса вместе с плитой.
Кроме поглощающего аппарата Р-2П допускается применение аппарата Р-5П (резиновый, пятый вариант, пассажирский), изображенного на рис. 1.67. Аппарат начинают собирать с установки в хомут 1 упорной плиты 2, плиты 3. Затем туда вводят резинометаллический элемент 4, плиту 6 и после ее сжатия устанавливают последний резинометаллический элемент. Плиты 3,5 и 6 надо располагать так, чтобы их боковые заплечики охватывали продольные стенки хомута. Чтобы исключить смещение резинометаллических элементов и их соприкосновение при сжатии аппарата со стенками тягового хомута, на плитах и листах элементов сделаны фиксирующие выступы и соответствующие углубления.
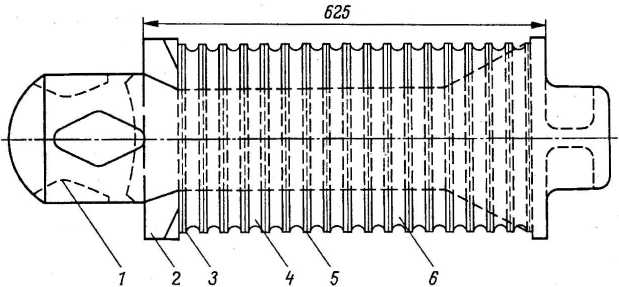
Рис. 1.67. Поглощающий аппарат Р-5П: 1 — хомут; 2 — упорная плита; 3, 5, 6 — промежуточные упорные плиты; 4— резинометаллический элемент
Перечислим основные неисправности аппарата: тяговый хомут — излом или износ; упорная плита — трещины, предельный износ; резинометаллический элемент (амортизатор) — отслоение резины, старение.
Усилие, воспринимаемое автосцепкой при сжатии вагонов, передается через ее хвостовик и нажимную плиту на резинометаллические элементы. Они сжимаются, поглощают удар автосцепки и ослабляют его.
Тяговый хомут отливают из стали. Он состоит из двух горизонтальных полос, соединенных по концам. В передней части хомута имеется окно для хвостовика автосцепки и отверстие для клина, соединяющего автосцепку с хомутом. Стальной клин устанавливают снизу, он удерживается своими заплечиками от подъема, от падения клин предохраняют два болта.