Автосцепка, автосцепное устройство, — служит для автоматического сцепления железнодорожной подвижного состава в поезд, передачи и смягчения продольных усилий и амортизации ударных нагрузок при. движении, остановках, а также при манёвре. В двух частях автосцепки, располож. на соединяемых вагонах, находятся элементы механизма сцепления, поглощающий аппарат, центрирующее (опорное) устройство, расцепной привод и элементы крепления и передачи нагрузки на раму вагона (через тяговый хомут, упорную плиту и др.)- Возможность взаимного сцепления частей автосцепки обеспечивается геометрией контура зацепления (замков) малого и большого зубьев.
Наибольшее распространение получила автосцепка с однозубым контуром замка (типа Джаннея) и с двухзубым контуром (типа Виллисона). Автосцепки могут иметь различных кинематической связи в контуре зацепления. В нежёстких автосцепках вертикальные перемещения в контуре в сцепленном положении не ограничены, в полужёстких — допускаются перемещения в некоторых пределах, в жёстких — не допускаются. Жёсткие автосцепки (типа Шарфенберга) специализированы и применяются на вагонах метрополитена и пассажирском подвижном составе постоянного формирования (электропоезда и дизель-поезда). Жёсткие автосцепки могут быть совмещены с соединителями поездных коммуникаций (воздушных, электрические, оптоволоконных).
Автосцепка заменила на подвижном составе винтовую стяжку, соединявшуюся вручную рабочим (сцепщиком), находившимся между вагонами. Вопрос об автосцепках на рус. ж. д. обсуждался впервые в 1898 на XX совещательном съезде представителей дорог.
Практическое решение этой задачи стало возможным в 30-е гг. 20 в. В 1932 разработана автосцепка типа СА-3 на осн. двухзубого контура зацепления (авторы Ф. Пухов, И. Н. Новиков, В. А. Шашков, В. Г. Голованов, под руководством Ф. Егорченко). Перевод подвижного состава сов. ж. д. на автосцепки начался в 1935 и завершён в 1957. автосцепка типа СА-3 (см. рис.) полностью автоматическая, изготовляется в нежестком и полужестком исполнениях.
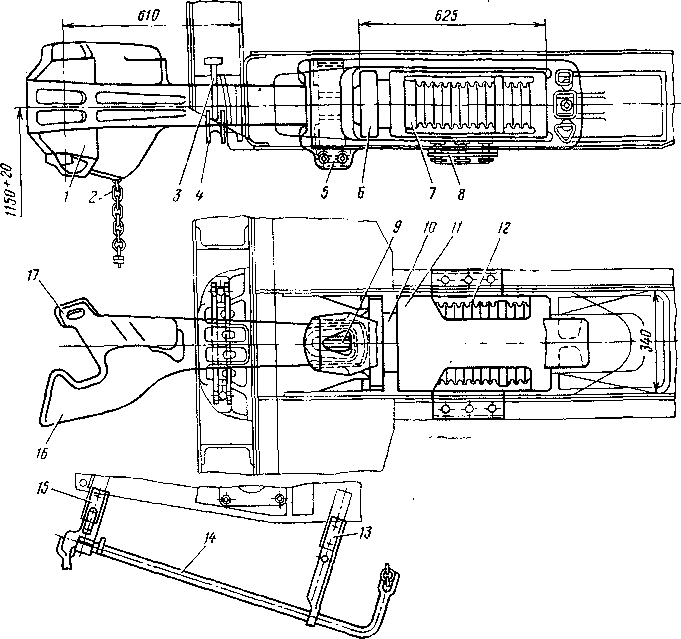
Рис. 49. Автосцепка СА-3 с поглощающим аппаратом: 1 — корпус автосцепки: 2 — цепь расцепного рычага; 3 – маятниковое устройство; 4 — балочка: 5 — тяговый хомут; 6 — упорная плита; 7 – корпус поглощающего аппарата; 5 — поддерживающая планка; 9 — клин; 10 — нажимная плита поглощающего аппарата; 11 — поглощающий аппарат; 12 — резинометаллические элементы: 13. 15 кронштейны: 14 – расцепной рычаг; 16 — большой зуб: 17 — малый зуб
Корпус и детали механизма сцепления (замка, замкодержателя, предохранителя, подъёмника и валика подъёмника) выполнены из стального литья. Взаимодействие деталей механизма обеспечивает автоматического сцепление при сжатии двух половин А. и автоматического восстановление готовности к сцеплению при их разъединении.
Расцепление производится вагонами. В автосцепках применяются следующие основные типы поглощающих аппаратов: пружинно-фрикционные, гидравлические, с резиновыми элементами и эластомерные (с вязкотекучим объёмносжимаемым рабочим телом). Грузовые вагоны имеют автосцепку, оснащённую пружинно-фрикционными поглощающими аппаратами, пассажирские — резино-металлическими.