Колесная пара. Осмотр и освидетельствование колесных пар в депо необходимо производить в полном соответствии с требованиями Инструкции по освидетельствованию, ремонту и формированию колесных пар локомотивов и электросекций (ЦТ/2306) и Правилами деповского ремонта электропоездов и секций (ЦТ/2614).
Во время эксплуатации могут встречаться следующие неисправности колесных пар. и их элементов:
- ослабление посадки бандажа на ободе центра колесной пары моторного вагона;
- ослабление бандажного кольца;
- ослабление посадки колеса на оси;
- образование трещин в различных частях оси, в ступице колеса, спицах, бандаже или ободе центра колеса;
- образование раковин, наплывов, выбоин или местного проката на поверхности катания колеса (ползуны);
- возникновение задиров, рисок в различных частях осп;
- вертикальный подрез гребня;
- неравномерный износ бандажей.
Об ослаблении бандажа свидетельствует:
- глухой дребезжащий звук при обстукивании молотком обода колесного центра и бандажа;
- нарушение целости слоя краски или выделение смазки, ржавчины по окружности в местах прилегания бандажа к ободу колесного центра;
- образование зазора между ободом колесного центра и упорным буртиком бандажа;
- несовпадение контрольных рисок на ободе колесного центра и бандажа.
Если возникло подозрение, что произошло ослабление посадки бандажа, необходимо на бандаже и ободе сделать отметки мелом и на каждой стоянке в оборотном пункте тщательно проверять взаимное расположение отметок. При проворачивании бандажа вагон нельзя допускать к дальнейшей эксплуатации.
Признаками ослабления посадки колеса на оси являются:
- выделение ржавчины или смазки вокруг ступицы с внутренней стороны или нарушение краски в месте сопряжения оси со ступицей;
- изменение расстояния (в условиях работы поезда на линии это обнаруживают по прижатию гребней обоих колес к рельсам или по набеганию тормозных колодок на гребни колес) между внутренними гранями бандажей;
- сдвиг контрольной цветной полосы, нанесенной на торец ступицы и на часть оси, в месте их прилегания;
- уменьшение расстояния от переходной галтели подступичной части оси до наружного торца ступицы колеса.
При обнаружении одного из указанных признаков необходимо тщательно проверить, нет ли других признаков ослабления посадки колеса на оси. Колесную пару со сдвигом ступицы запрещено допускать к эксплуатации.
Об образовании трещин в подступичной части оси можно судить по выделению ржавчины в виде мелкой красноватой пыли, нарушению целости слоя краски или вздутию краски бугорком в месте сопряжения оси со ступицей и образованию зазора между осью и ступицей. При обнаружении одного из указанных признаков следует тщательно проверить подступичную часть оси и определить, нет ли других признаков образования трещин.
Если краска в месте сопряжения оси со ступицей вздулась бугорком, необходимо тонкой иглой поднять слой краски бугорка и тщательно осмотреть это место. Наличие на оси под бугорком мелкой металлической пыли указывает на образование трещин в подступичной части оси.
Ультразвуковую дефектоскопию оси можно осуществить без выкатки колесных пар из-под вагона и демонтажа буксовых подшипников. Для этого необходимо отвернуть болты, крепящие крышку буксы, и снять ее. Затем отвернуть болты, крепящие стопорную планку, и также снять ее. Отвернуть гайку и ввести в канавку, расположенную между шейкой и резьбовой частью оси, щуп дефектоскопа.
Ультразвуковую дефектоскопию осей без выкатки колесных пар следует производить в соответствии с информационным письмом № 433 Всесоюзного научно-исследовательского института железнодорожного транспорта «Ультразвуковой контроль подступичной части вагонных осей» (Трансжелдориздат, 1958 г.).
Выявление трещин в колесной паре, выкаченной из-под вагона, необходимо производить до удаления с нее пыли, грязи и краски, так как после очистки характерные признаки трещин становятся малозаметными или совсем незаметными.
Чтобы убедиться в отсутствии трещин в оси, необходимо после очистки от пыли и грязи проверить шейку, подступичную и среднюю части оси дефектоскопом.
Магнитный контроль осей необходимо выполнять в соответствии с Инструкцией по магнитному контролю ответственных деталей локомотивов и вагонов дизель-поездов и электропоездов в депо и на локомотиворемонтных заводах (ЦТ/1835).
При обнаружении трещин следует руководствоваться Инструкцией по освидетельствованию, ремонту и формированию колесных пар локомотивов и электросекций (ЦТ/2306) и Правилами деповского ремонта электропоездов и электросекций (ЦТ/2614).
Редуктор. При эксплуатации возможны следующие неисправности редуктора: образование трещин и излом зубьев ведущей шестерни и ведомого колеса; ослабление призонных болтов, крепящих венец ведомого зубчатого колеса к ступице; выход из строя роликовых подшипников узла ведущей шестерни и опорных подшипников корпуса редуктора; ослабление болтов, соединяющих половины корпусов редуктора, болтов, крепящих корпус редуктора к опорному стакану, и болтов крышек редуктора; образование трещин в корпусе редуктора.
При первом малом периодическом ремонте после выпуска поезда заводом-изготовителем необходимо произвести тщательный осмотр крепежных деталей редуктора, проверить затяжку болтов. Ослабленные болты необходимо подтянуть. Во избежание срыва головок болтов и резьбы затягивать болты следует, пользуясь ключами только с рукояткой стандартной длины (усилие, приходящееся па рукоятку ключа, не должно превышать 20—25 кг).
Одновременно через люк в корпусе редуктора осматривают зубья передачи, определяя характер их износа. Смазку в корпусе редуктора необходимо сменить.
Последующие ревизии зубчатой передачи производят при большом периодическом ремонте с обязательной выкаткой тележки и разборкой редуктора.
Регулярно, при каждом профилактическом осмотре, проверяют состояние токосъемного кольца и уплотнения корпуса узла заземления. Это кольцо и корпус очищают от графитовой пыли и смазки.
При больших периодических ремонтах производят очистку корпуса редуктора от грязи и смазки и зубчатой передачи от смазки. Определяют, нет ли трещин в венце зубчатого колеса и шестерни. При обнаружении лучевых трещин или вмятин, выкрошенных мест и трещин на поверхности зацепления надо заменить зубчатый венец (колесную пару) или шестерню. Проверяют крепление зубчатого венца ведомого колеса, а также износ зубьев. Максимальный износ зубьев по начальной окружности не должен превышать 1,5 мм на одной стороне.
Зачищают все заусенцы и наплывы на зубьях, производят ревизию опорных подшипников редуктора и подшипников узла малой шестерни, заменяют смазку в опорных подшипниках узла малой шестерни. Проверяют уплотнения редуктора, уплотнения корпуса узла заземления и очищают токосъемное кольцо и корпус щетки заземления от графитовой пыли и смазки.
Смазку зубчатой передачи производят в соответствии с картой смазки (приложение 1). Корпус редуктора заполняют смазкой через отверстия в приливе нижней половины корпуса. Уровень смазки должен быть на 10 мм ниже края отверстия.
Смазку опорных подшипников редуктора осуществляют через отверстие во фланце верхней половины корпуса. Отверстия закрывают резьбовой пробкой. Для смазки подшипников узла ведущей шестерни предусмотрены специальные смазочные каналы в крышках.
Добавлять смазку в подшипники ведущей шестерни и опорные подшипники редуктора необходимо регулярно в соответствии с картой смазки (приложение 1).
Подвеска редуктора. Подвеску редуктора следует осматривать при каждом профилактическом осмотре. При осмотре следует также определить, нет ли в стержне подвески редуктора трещин. При обнаружении трещин необходимо подвеску заменить. После замены ее нужно отрегулировать зазоры между предохранительной вилкой подвески и специальной гайкой предохранительной шпильки (зазор должен составлять 20 мм под тарой вагона для подвесок с прямым стержнем).
Необходимо также проверить затяжку специальных гаек болта подвески редуктора. Гайки должны быть плотно затянуты и застопорены.
Буксы и буксовые направляющие. Ревизии букс и роликовых подшипников следует производить в соответствии с Правилами деповского ремонта секций электропоездов постоянного тока и Инструкцией по содержанию и ремонту роликовых подшипников локомотивов и моторвагонного подвижного состава (ЦТ/2361). При эксплуатации буксы в случае неисправности перегреваются. Поэтому сразу же после остановки поезда в пунктах оборота необходимо проверять на ощупь нагрев букс. Температура букс не должна превышать 65° С.
Перегрев букс происходит главным образом по следующим причинам:
- неисправность роликовых подшипников;
- отсутствие зазора между корпусом буксы и лабиринтным воротником;
- отсутствие смазки или излишек ее, затрудняющий работу роликов и вызывающий повышенное трение;
- самоотворачивание торцовой гайки, крепящей подшипники.
Последнее может произойти из-за непрочного закрепления болтами стопорной планки, излома проволоки, контрящей эти болты, или поломки стопорной планки.
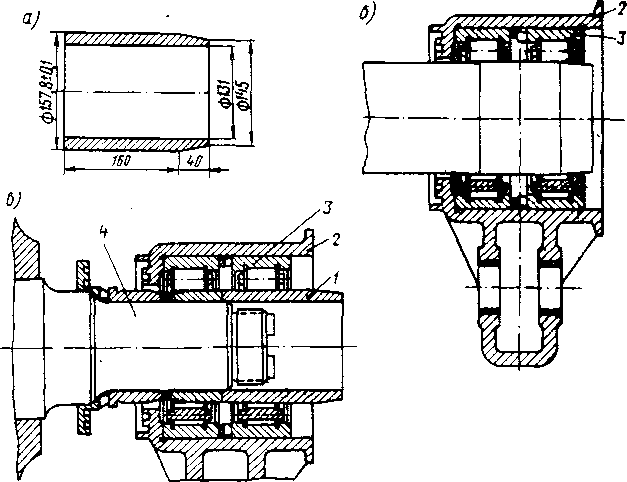
Рис. 15. Монтажная втулка (а) и схемы (б, в), поясняющие ее применение: 1 – монтажная втулка; 2 — корпус буксы; 3 — подшипники; 4 — ось
При эксплуатации возможны следующие неисправности буксовых подшипников:
- образование трещин на поверхности катания роликов или на их торцах;
- шелушение металла на поверхности катания роликов, беговых дорожках внутренних или наружных колец подшипников;
- разрушение роликов и сколы по их фаске: проворачивание внутренних подшипниковых колец или их разрыв;
- разрушение сепараторов.
Если в процессе эксплуатации необходимо заменить подшипники, то сборку буксового узла с новыми подшипниками следует производить при помощи монтажной втулки, как показано на рис. 15.
Наличники буксовых направляющих должны быть жестко закреплены, болты и винты, крепящие наличники, туго затянуты, прорезные гайки зашплинтованы, а разрезные концы винтов слегка разведены. Суммарные зазоры между наличниками буксовых направляющих и буксами не должны превышать 6 мм в продольном и 8 мм в поперечном направлениях. Эксплуатация тележек с большими зазорами запрещается.
Для новых колесных пар суммарные зазоры между наличниками буксовых направляющих и буксами должны быть равны 1—3 мм в продольном направлении и 2—4 мм в поперечном. Перекос или заклинивание букс между направляющими недопустимы.
Корпуса и крышки букс не должны иметь трещин и изломов.
На каждом профилактическом осмотре необходимо проверять предварительный натяг пружин буксовых фрикционных гасителей. Предварительный натяг проверяют по зазору между стаканом и нажимной крышкой гасителя, который должен составлять 7±0,5 мм.
Величина предварительного натяга резиновых шайб-амортизаторов обеспечивается дистанционными втулками.
Допускают износ фрикционных накладок до толщины 4 мм, а металлических деталей — до 6 мм.
Упругая муфта. В эксплуатации возможны следующие неисправности упругой муфты: распрессовка фланцев двигателя или шестерни, повреждение упругой оболочки или трещины верхнего слоя резины в месте крепления к металлическим поверхностям, ослабление болтов, крепящих упругую оболочку.
Муфты, имеющие одну из указанных неисправностей, к эксплуатации допускать нельзя. Следует иметь в виду, что повреждение нерабочего (декоративного) поверхностного слоя резины не считается повреждением упругой оболочки. Муфту допускают к эксплуатации, если повреждение не распространилось на несущий (кордовый) слой оболочки, при этом резину в месте повреждения следует срезать ножом с плавным переходом по краям среза. Полную разборку муфты следует производить в следующем порядке:
- выкатить тележку из-под вагона (при необходимости);
- отвернуть болты, крепящие упругую оболочку к фланцу двигателя; сжать в осевом направлении упругую оболочку па величину, позволяющую вывести втулки разрезного кольца из отверстий фланца двигателя;
- опустить редуктор, отвернув верхнюю гайку подвески;
- вынуть освободившиеся полукольца из полости упругой оболочки;
- вывернуть из втулок полуколец болты, крепящие упругую оболочку к фланцу шестерни, на величину, позволяющую снять шайбы с прорезью;
- снять полукольца, вывернув втулки полуколец из отверстий фланца шестерни, и спять упругую оболочку;
- при необходимости специальным приспособлением спрессовать фланцы двигателя и шестерни.
При разборке муфты необходимо тщательно осматривать упругую оболочку, детали крепления и посадочные поверхности.
Монтаж муфты производят в следующем порядке. Притирают конусные поверхности фланцев двигателя (шестерни) и валов двигателя (шестерни). Притертая поверхность при проверке по краске должна составлять не менее 90% сопрягаемой конусной поверхности вала. Нагревают фланцы двигателя (шестерни) в масляной ванне при температуре +140°С и выдерживают при этой температуре. Вынимают фланцы из ванны, протирают насухо поверхности конусных отверстий и сажают фланцы на вал двигателя (шестерни). Фланец должен сесть на 1,7—2,0 мм глубже, чем при посадке в холодном состоянии.
Затем устанавливают на фланец шестерни упругую оболочку, заводят полукольца с втулками и завернутыми в них болтами в полость оболочки, а концы втулок в отверстия фланца.
В цековки фланца под головки болтов с шайбами устанавливают шайбы с прорезью и затягивают болты. Затяжку болтов производят ключом с рукояткой длиной не менее 750 мм; к рукоятке необходимо прикладывать усилие, примерно равное 30 кг. Равномерность затяжки упругого элемента и отсутствие перекоса определяют замерами через отверстие 0 5 мм. Разница в замерах нс должна превышать 2 мм. Заводят в упругую оболочку две половины разрезного кольца и насаживают на фиксаторы. Устанавливают фиксаторы по схеме, показанной на рис. 14. Поднимают корпус редуктора до тех пор, пока не совпадут оси вала двигателя и вала шестерни.
Сжимают упругую оболочку в осевом направлении на величину, позволяющую завести концы втулок разрезного кольца в отверстия фланца двигателя. Закрепляют упругую оболочку болтами, под головки которых устанавливают шайбы с прорезью. Затяжку болтов производят, как было указано выше. С целью предотвращения самоотворачивания производят контровку болтов проволокой.
При эксплуатации вагонов, имеющих упругие муфты, необходимо регулярно, на каждом профилактическом осмотре, тщательно проверять затяжку болтов, крепящих оболочку к фланцам, и состояние упругой оболочки.
Выше описаны полная разборка и сборка упругой муфты.
При частичной разборке (например, при смене тягового двигателя, смене упругой оболочки и др.) выполняют работы, обеспечивающие данный вид частичной разборки, в последовательности, указанной для полной разборки. Сборку в этом случае производят в обратной последовательности.
После каждой разборки и сборки необходимо проверить размер 166+6 мм и смещение фланцев друг относительно друга (3+1 мм).
В случае если эти размеры не соответствуют указанным, нужно установить их перемещением двигателя вдоль его оси и затяжкой стержня подвески редуктора (3+1 мм).
Категорически запрещается допускать в эксплуатацию неправильно отрегулированную муфту.
Рама тележки и детали центрального подвешивания. В эксплуатации необходимо систематически вести наблюдение за рамой тележки и деталями подвешивания: подвесками, скользунами, продольными тягами, гидравлическими гасителями колебаний и всеми болтовыми соединениями.
Особое внимание при осмотрах следует обращать на поперечные балки, кронштейны, подвески редуктора, продольные балки в местах отверстий для подвесок центрального пчдвешивания и в местах буксовых проемов, узлы соединения продольных балок с поперечными и на надрессорный брус.
Запрещается эксплуатация рам и надрессорного бруса тележек с трещинами.
Гайки болтов крепления скользунов тележек и кузова должны быть плотно затянуты и зашплинтованы.
Скользун-вкладыш, выполненный из древеснослоистого пластика ДСП-Г, должен выступать из коробки на высоту не менее 3 мм, поверхность его должна быть чистой, гладкой, без задиров и выкрашиваний, толщина скользуна должна быть не менее 20 мм.
Допускают к эксплуатации скользуны с мелкими питингами на поверхности трения, если они занимают не более 60% поверхности и глубина их не превышает 3 мм. При этом поверхность стального скользуна кузова должна быть гладкой, без задиров, рисок и раковин.
Удалять дефекты с поверхности скользунов разрешается механической обработкой: фрезеровка скользунов из ДСП-Г и шлифовка стальных скользунов.
При износе вкладыша до толщины 28 мм его заменяют.
Категорически запрещается эксплуатация тележек с изломами или трещинами в деталях центрального подвешивания. Подвески центрального подвешивания следует периодически подвергать магнитному контролю согласно Инструкции по магнитному контролю ответственных деталей локомотивов и вагонов дизель-поездов-и электросекций в депо и на локомотиворемонтных заводах (ЦТ/1835, 1955 г.).
Допустимые величины износов рамы тележки и деталей центрального подвешивания указаны в Правилах деповского ремонта электропоездов и электросекций (ЦТ/2614).
Пружины центрального подвешивания должны находиться в своих гнездах. Не допускаются к эксплуатации пружины с изломом или трещинами в каком-либо витке и пружины с просадкой выше установленных норм. Смену пружин центрального подвешивания под вагоном рекомендуется производить, используя специальные гидравлические домкраты, в следующем порядке:
- подвести под поддон два домкрата и, сжимая пружины, поднять поддон на величину, позволяющую снять серьги с валиков подвесок;
- на продольную балку рамы тележки, под шкворневую балку кузова установить распорный деревянный брусок или другое приспособление;
- снять с валиков подвесок серьги и опустить поддон с пружинами;
- заменить неисправную пружину.
После замены пружины сборку центрального подвешивания производят в обратном порядке.
При замене пружин центрального подвешивания на выкаченных из-под вагона тележках используют стяжные болты, струбцины или пневмоприжимы для подтягивания поддона к раме, при этом освобождаются серьги подвесок. Смену пружин ведут в вышеизложенной последовательности.
В центральном подвешивании устанавливают гидравлические гасители колебаний (амортизаторы) производства Калининского вагоностроительного завода.
Ревизию гидрогасителей необходимо производить при плановых ремонтах вагонов в депо через каждые 100 тыс. км пробега, но не реже чем через каждые шесть месяцев, а контрольные проверки на вагонах вручную один раз в промежутке между ревизиями, а в зимнее время — через месяц.
При выявлении неисправностей гидрогасителей во время контрольной проверки следует произвести их ревизию. Порядок проведения ревизии гидравлических гасителей колебаний изложен на стр. 37.
Выкатка тележки. При выкатке тележки сначала следует отвернуть гайку шкворня, снять ее и упорную шайбу. Затем отсоединить воздушные рукава и электропровода от тягового двигателя, соединительные рукава тормозных цилиндров, а на тележке со стороны привода ручного тормоза отсоединить трос от двуплечего рычага. После этого домкратами поднимают кузов и выкатывают тележку. Тележки электропоезда ЭР2 с повышенным статическим прогибом не предусмотрены для подкатки под вагоны электропоездов других серий и электропоездов ЭР2 до № 514.
Подбор пружин на моторных тележках имеет особое значение в связи с большим прогибом (большой гибкостью) пружин. Пружины следует подбирать в зависимости от веса брутто вагона и его развески по концам в строгом соответствии с технической документацией на тележку данного типа.